Technical Specifications of Wire Rod Coil Decaling Machine
- Diameter of the wire: Φ 4~Φ 40mm
- Inner diameter of coil: Φ 800-1100mm
- Outer diameter of coil: Φ1200-1400mm
- Maximum load capacity mandrel :2700kg
- Wire rod coil handing type: cantilever mandrel loading ( One cantilever mandrel inside the blasting chamber will clockwise rotate 15s and then counterclockwise 15s which controled by PLC during blast descaling, the rotation time for each direction is adjustable. while the other Outdoor cantilever mandrel is loading and unloading )
- Productivity: 7-15min/time
- Effective length of mandrel:3800mm-5500mm(can be customized)
- Rotation speed: 10-20 r/min ( frequency control )
The technical data is not binding and may be subject to change.
Depending on the type of parts, production method, etc., further machine types and measurement specification sheets upon request.
Benefits and Features of Wire Rod Coil Decaling Machine
The Wire Rod Coil Decaling Machine is special designed for blast cleaning wire rod coils. It uses the blasting process to remove the rust, heat scale and Corrosion from the surface of the wire rod coil. The surface derust grade can reach to Sa2.5 and roughness grade can reach to Ra6.3μm to Ra12.5μm after shot blasting process. Compared with the pickling treatment method, it has the features of economy, environment-friendly and high efficiency.
Applications of Wire Rod Coil Decaling Machine
Surface preparation for coil wire rod:
Rust and Heat Scale removal
Corrosion removal
Cleaning
Wire Rod Coil Decaling Machine
The Wire Rod Coil Decaling Machine is special designed for blast cleaning wire rod coils. It uses the blasting process to remove the rust, heat scale and Corrosion from the surface of the wire rod coil. The surface derust grade can reach to Sa2.5 and roughness grade can reach to Ra6.3μm to Ra12.5μm after shot blasting process. Compared with the pickling treatment method, it has the features of economy, environment-friendly and high efficiency.
This machine adopt the unique “revolving door + 3.8 meters double cantilever mandrels”to load the wire rod in coils, it implement dual-station working mode, and greatly increase the production capacity of the equipment.
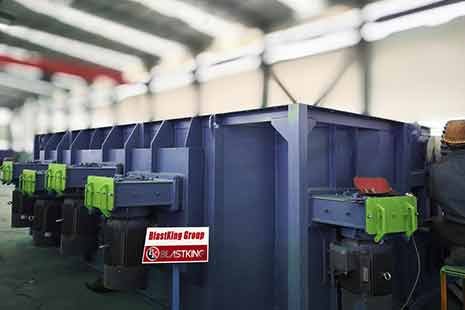
Cantilever mandrel is made by special alloy steel, the action of the mandrel of “up and down + swing around + clockwise and anticlockwise rotation” are perfectly combined to reach to the throughly blast cleaning effect during the shot blasting process. Due to the reasonable blast wheel arrangement and the above mentioned, the inner and outer surfaces of the wire rod coil can be effectively blasted cleaning by blasting media. The whole machine system is controlled by PLC which can easily and reliably operate.
Shot Blasting Cabinet
The blasting chamber is fabricated by high strengthened steel plates and profile steel which ensures adequate intensity and rigidity of the machine. ,blast wheels layout adopt 3-D dynamic simulation design, which ensures optimal shot blasting angle and distance.
As with all BlastKing Blast Machines adopt easy replaceable high manganese steel guard liner on hot blasting zone, which is hard enough to deal with the shot blasting hardness up to 60HRC. The overlapped liner blocks are installed inside the blasting chamber which eliminate any possibility that the high speed blasting media will hit the blasting chamber directly.
High impact toughness can make full use of the reflection kinetic energy of shot to continue to blast cleaning the surface of work piece, so greatly enhance the cleaning efficiency and quality.
High chrome wear resistant perforated saddle plate are deployed at the bottom of the blasting chamber which ensure the used blasting media will appropriately get into the abrasive recycle system and prevent any damages to the bottom screw conveyor.
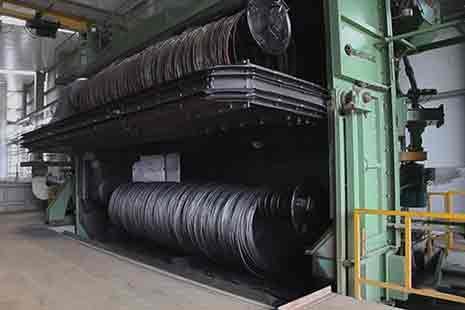
Cartridge Filter Unit
Each BlastKing machine is equipped with multiple cartridge filters. These filters are necessary to remove any impurities from the air used to blast resulting in a more even, direct, and effective blast.Benefits experienced with the BlastKing’ cartridge filters:
Large distance between folds in each cartridge filter leads to precise cleaning and better air pressure.
The impact separator within the cartridge filter unit ensures that the broken down fines are separated (which protects the filter cartridge against unnecessary wear).
The cartridge filters clean the cartridge automatically using an air pressure pulse, the intensity and duration of the pulse can be adjusted according to the type and amount of dust.
Pressure difference is monitored to automatically set the cleaning cycle increasing the life time of the cartridge and saves compressed air.
Easy exchange of cartridge filters.
Correct contact pressure.
Low compressed air consumption.
Constant cleaning, from top to bottom, due to conical design of the cartridge filter.
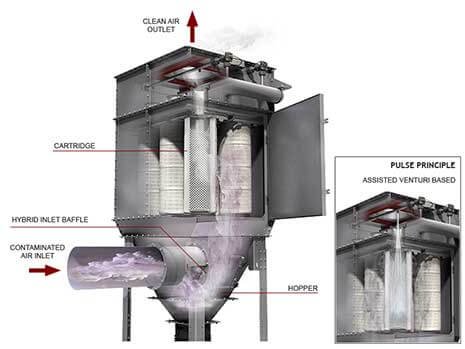
BlastKing ORICA Wheel
BlastKing group have the patented technology of the direct drive blasting turbine which motor power from 22kw to 75kw.
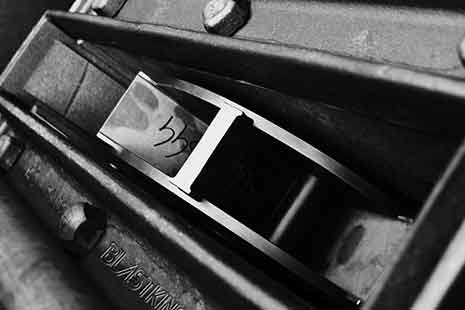
BlastKing Abrasive dosing unit
The abrasive dosing unit is abrasive flow control mechanism, The unit’s opening and closing angles can be controlled electrically or pneumatically. The abrasive flow rate is displayed on the ammeter of the electrical system. The unit adopts the German AGTOS abrasive dosing technology which use pneumatic controlling pull-type opening and closing technology.
Compared to the traditional fan-shaped open and close structure, it has the advantages of long life, maintenance-free, sealing and performance more superior and powerful. The abrasive flow rate can be adjusted, and the dynamic conditions can be showed on the ammeter.
The abrasive dosing unit is without stuck and blasting media leakage conditions, and the unit opening/closing conditions can be detected during operation, which will avoid the blasting media hit the chamber directly if the workpieces are not in place.
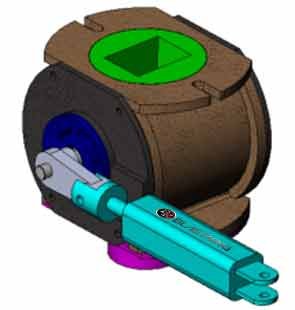
References to Wire Rod Coil Decaling Machine
Installation, Post-sales, Training & Safety
BlastKing Provide turnkey installation for the shot blaster. DIY installation by customer is also available according to the comprehensive documents, videos and drawings which provide by BlastKing, our engieers team also can provide real-time installation guidance.
The successful implementation of any blasting equipment is based upon the total commitment and dedication to the process. BlastKing’s field technicians are involved in the installation and training of the programmer and operator at the customer’s site or at BlastKing’s training facility. BlastKing has developed a complete program of maintenance training seminars. These are scheduled not only for new users but also for existing users. This structure is ideal for customers to send new employees so they can become more conversant with all BlastKing’s equipment.
Guarantee time of shot blasting machine will be one to five years. Technical support will be during the whole blasting machine life. Consumable spare parts will be supplied periodically.
All the equipment from BlastKing is conformity with CE&BV standard, and our factory have ISO9001, ISO14001 certification.
General emergency stop button is on all the BlastKing’s control panel. And sub emergency stop buttons are on conveyor systems. Detectors on the blast wheel covers, blasting chamber windows, elevators, separators will protect safety of the operators. Dust collection unit of shot blast machine dust emisssions is under 3mg/m3 which also bring dust free working environment.