1. What is a Blasting Room?
A blasting room is a confined space specifically designed for abrasive processes like sandblasting or shot blasting. It serves as a controlled environment where abrasive materials are forcefully propelled against a surface, effectively removing contaminants or preparing the surface for subsequent treatments. The essential components of a blasting room encompass an abrasive material storage system, a blasting device, and a well-designed ventilation system.
Turbocharge Your Productivity in the Blasting Room
2. Main Features of a Performance Blast Room
A performance blasting room is a sophisticated facility designed for efficient and effective abrasive blasting processes. It comprises five essential components, each contributing to the overall functionality and success of the blasting operation.
Chamber Design:
The blasting chamber serves as the central space for the abrasive blasting process. It is equipped with robust doors, ensuring secure containment during blasting. The chamber is typically lined with heavy-duty steel plates on all surfaces to withstand abrasion from ricocheting abrasive particles. Adequate lighting is incorporated to enhance visibility for operators. Additionally, correctly sized air entry and exit plenums are integrated to facilitate efficient ventilation while preventing the escape of abrasive material.
Dust Collection and Ventilation System:
A crucial element of the performance blasting room is the dust collection and ventilation system. This system ensures a continuous and controlled airflow within the chamber, keeping dust levels low for improved operator visibility. It plays a pivotal role in rapidly clearing the room of dust when the blasting operation concludes. The efficient removal of dust contributes to a safer working environment and enhances the overall quality of the blasting process.

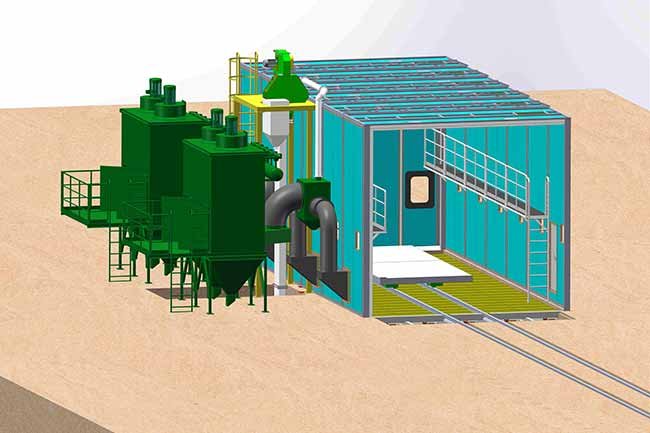

Abrasive Recovery System:
Positioned typically beneath the floor of the chamber, the abrasive recovery system is responsible for collecting and conveying spent abrasive to a central point. This central collection facilitates recycling and cleaning of the abrasive material. An efficient recovery system can automatically recover abrasive from the entire floor or specific areas based on the chamber’s design, optimizing the use of abrasive material.
Abrasive Recycling and Cleaning Unit:
This unit is dedicated to cleaning the used abrasive material, separating it from dust, fines, paint flakes, and other contaminants. The cleaned and reusable abrasive is then stored within the system, ready for subsequent blasting operations. The abrasive recycling and cleaning unit plays a crucial role in maintaining the quality of the abrasive material and ensuring cost-effective and sustainable blasting practices.
Blasting Pots, Hoses, and Nozzles:
The selection of appropriate blasting pots, hoses, and nozzles is vital in aligning with the specific requirements of the blast room function. Multiple outlets are typically installed to enable more than one operator to engage in continuous blasting. This feature enhances productivity and ensures a seamless and uninterrupted abrasive blasting process.
In summary, a performance blasting room integrates these five key components to create a controlled and efficient environment for abrasive blasting. The thoughtful design and integration of these elements contribute to the safety, quality, and sustainability of the entire blasting process.
Elevate Your Business with Blasting Room Brilliance
Is downtime costing you money? Are traditional methods falling short on quality? Do you desire a solution that’s both swift and sophisticated?
Supercharge your business growth with the Blasting Room advantage. Discover the secret weapon that industry leaders use to stay ahead. Don’t just keep up; lead the way!
Call us today at +86 135 8931 7685
3. Applications of Blasting Room
Blasting rooms find versatile applications across various industrial processes, particularly in surface preparation. The efficacy of blasting rooms is evident in their ability to cater to the needs of diverse materials and structures, making them indispensable in industries such as construction, manufacturing, and metal fabrication.
- Surface preparation is a critical phase in the production of beams, metal sheets, pipes/tubes, slabs, and large welding constructions. Blasting rooms play a pivotal role in ensuring that these surfaces are thoroughly cleaned and prepared for subsequent processes. By effectively removing contaminants, rust, and old coatings, blasting rooms contribute to enhancing the quality and longevity of the finished products.
- In addition to surface preparation, blasting rooms excel in smoothing applications, addressing imperfections like pickled or eroded surfaces, machining lines, and other irregularities. The abrasive nature of the blasting process proves highly effective in achieving smooth and uniform surfaces, ensuring the integrity of the materials and facilitating seamless downstream operations.
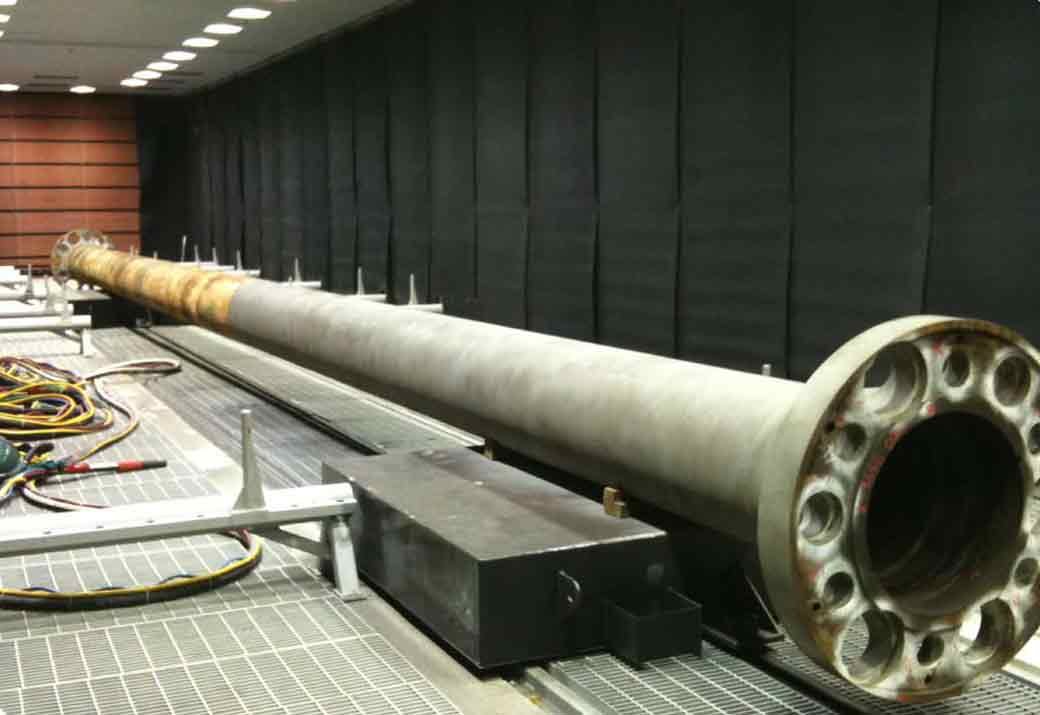
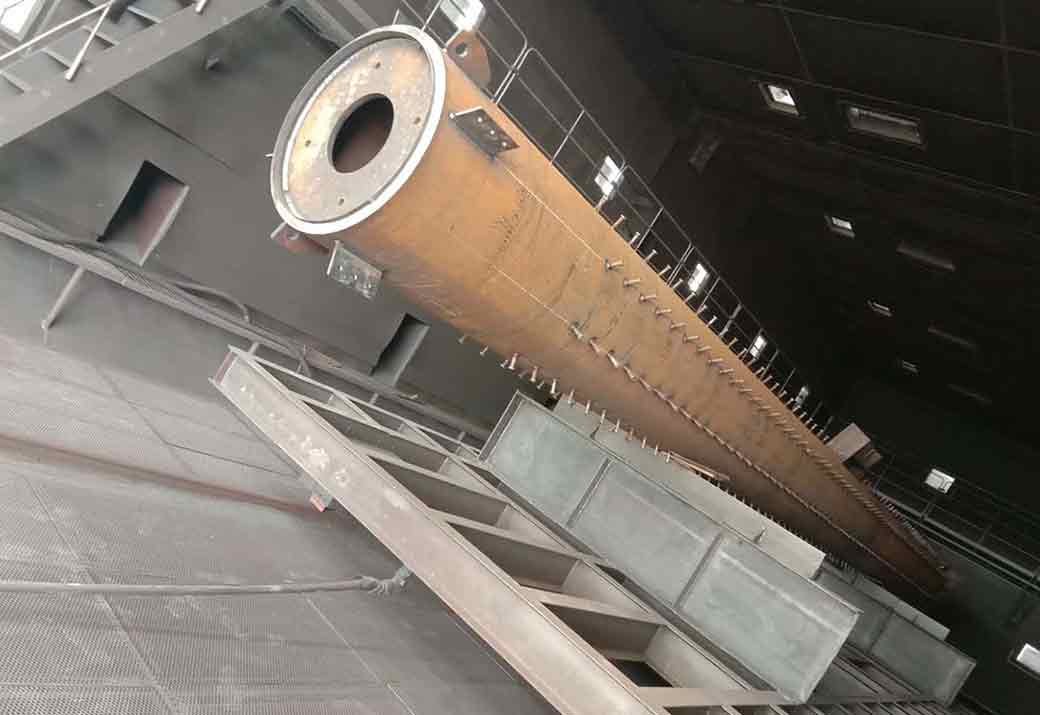

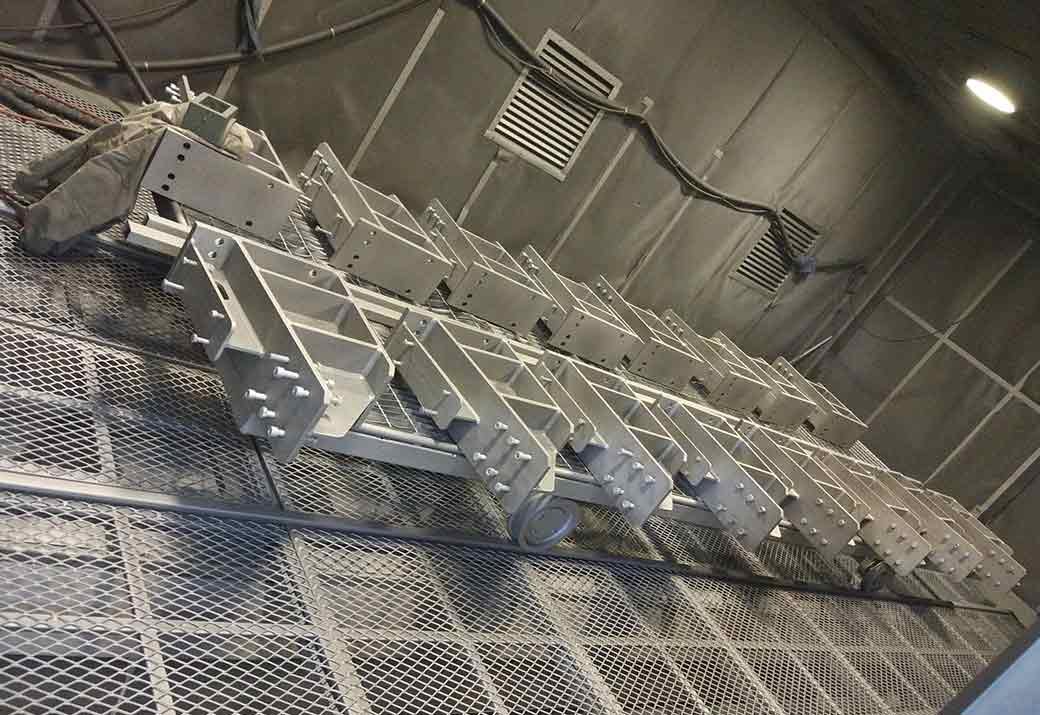
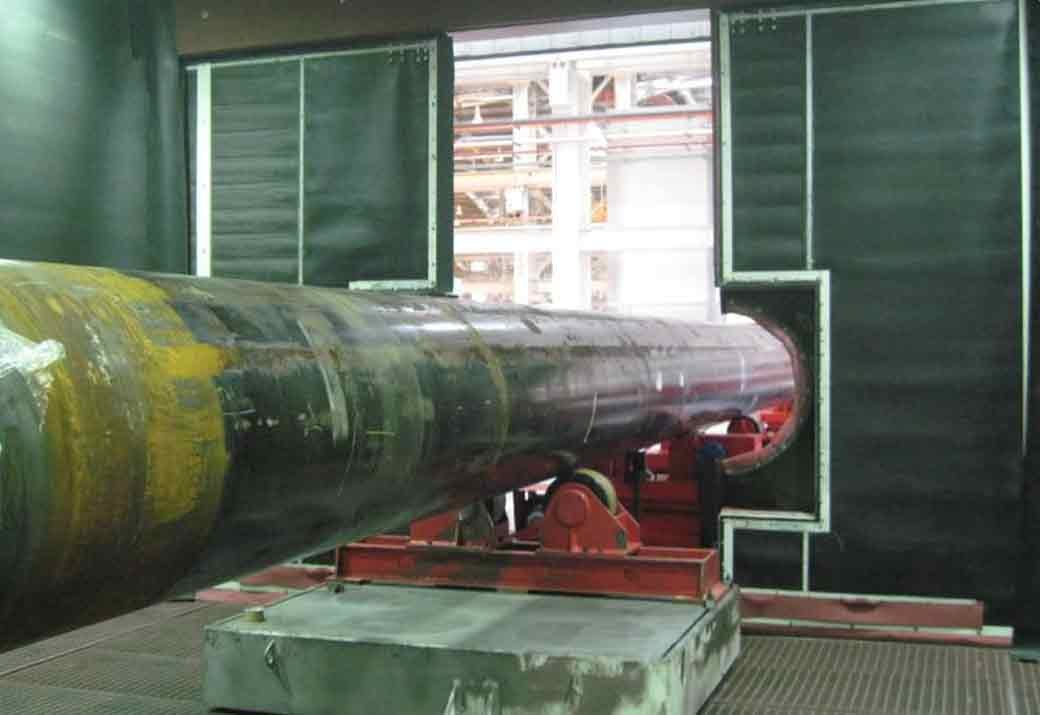
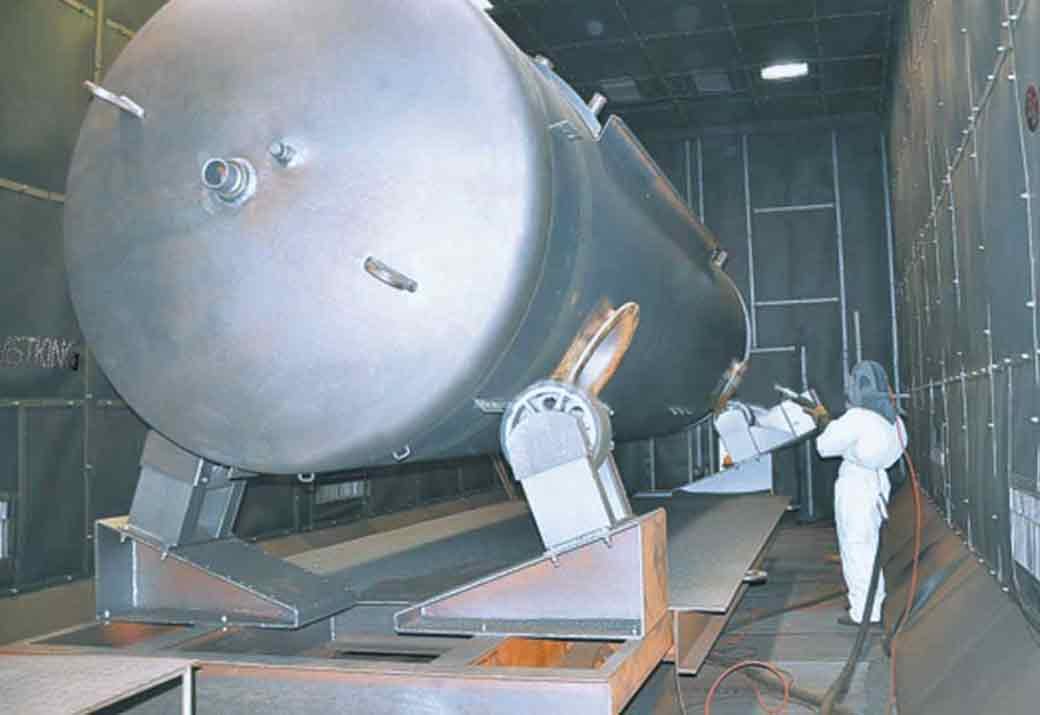
- Decorative blasting represents another dimension of the blasting room’s capabilities. Particularly adept at handling light metals, stainless steel, copper, brass, and other aesthetically significant materials, blasting rooms contribute to the creation of visually appealing surfaces. This makes them indispensable in industries where both functionality and aesthetics are paramount, such as architectural and artistic metalwork.
- Peening, a specialized application of blasting, involves bombarding parts exposed to high stress with abrasive materials. This process is especially crucial for components like torsion bars, where enhancing resistance to fatigue and improving durability are essential. Blasting rooms provide a controlled environment for peening, ensuring the desired surface treatment and mechanical properties are achieved with precision.
- De-burring, another key application, involves the removal of sharp edges and burrs from materials like flame-cut, sawed, and stamped parts. Blasting rooms prove instrumental in streamlining this process, eliminating potential safety hazards and ensuring the final product meets quality standards.
In summary, blasting rooms emerge as indispensable tools in the industrial landscape, offering a wide array of applications ranging from surface preparation for diverse materials to achieving smooth, decorative, and functionally enhanced surfaces. Their versatility makes them a cornerstone in various sectors, contributing significantly to the overall quality and performance of fabricated components and structures.
Uncover Hidden Potential in the Blasting Room
4. Why install a blast room?
Installing a blast room offers a multitude of advantages, encompassing both economic and environmental benefits. One of the primary advantages is the elimination of weather constraints. Unlike outdoor blasting, a blast room provides a controlled environment where abrasive processes such as sandblasting or shot blasting can occur regardless of weather conditions. This 24/7 accessibility allows for continuous operation, enabling businesses to achieve higher productivity levels and meet tight customer deadlines.
The controlled environment within a blast room contributes significantly to achieving a consistent quality of work. The ability to regulate factors such as temperature, humidity, and lighting ensures that the blasting process remains stable, leading to uniform results on treated surfaces. This consistency is vital for meeting industry standards and exceeding customer expectations.
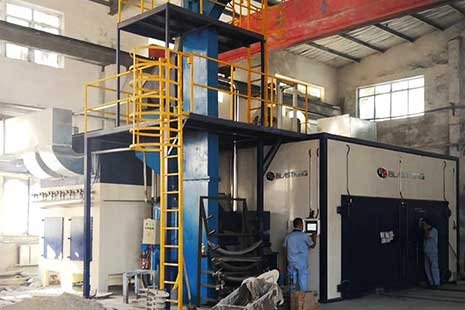
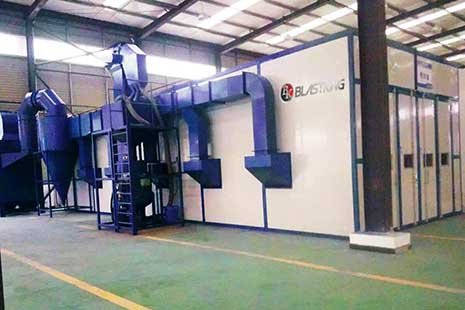
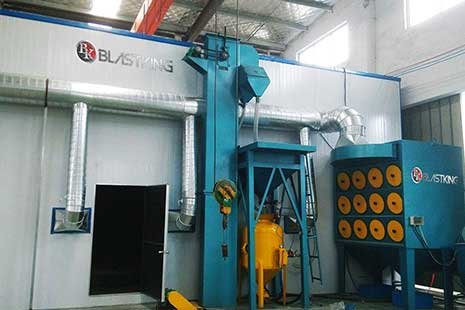
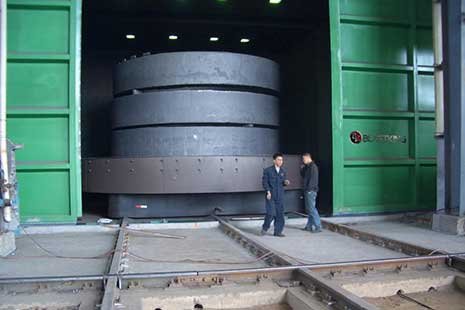
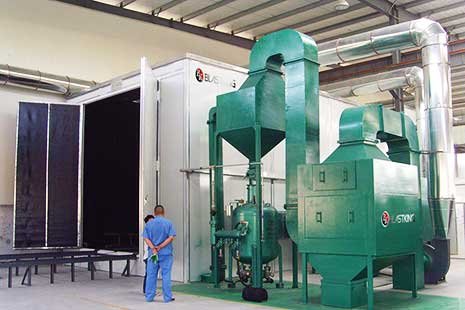

Moreover, blast rooms often incorporate automatic abrasive recycling systems. These systems facilitate the use of recyclable abrasives, resulting in a drastic reduction in costs. Not only does this lower the expenses associated with purchasing abrasives, but it also minimizes handling and disposal costs. The integration of recycling systems aligns with sustainability practices, showcasing a commitment to environmentally friendly operations.
By confining all dust generated during the blasting process within the blast room, the overall site environment becomes cleaner and tidier. This containment not only enhances the safety of the work environment but also contributes to improved air quality. Additionally, the controlled environment minimizes the impact on neighboring areas, making the overall site more agreeable for nearby residents and businesses.
In summary, the installation of a blast room provides a comprehensive solution for businesses engaged in abrasive processes. It ensures uninterrupted operation, enhances the quality of work, reduces costs through recycling systems, and promotes a cleaner and safer overall working environment. The decision to install a blast room reflects a commitment to efficiency, sustainability, and positive relations with the surrounding community.
Struggling to Innovate? Break Free with Blasting Room!
Are you facing creative roadblocks? Do productivity issues hinder your success? Is your business growth plateauing? Unleash the Blasting Room, the remedy to your challenges!
Call us today at +86 135 8931 7685
5. Recovery system
Recovery systems in abrasive blasting operations come in various configurations, ranging from 100% area under-floor systems to simpler sweeping hopper systems. The choice of a recovery system has a direct impact on productivity, operator involvement, and the overall efficiency of the abrasive blasting process.
A recovery system with 100% floor recovery is designed to maximize productivity by ensuring that operators never need to handle spent abrasive. This system effectively collects all the spent abrasive that falls through the floor grating. An alternative to this is a 25% or 50% floor area recovery system, which necessitates daily operator sweeping to recycle all abrasives. While these systems may be more cost-effective initially, they require additional manual effort and can impact productivity.
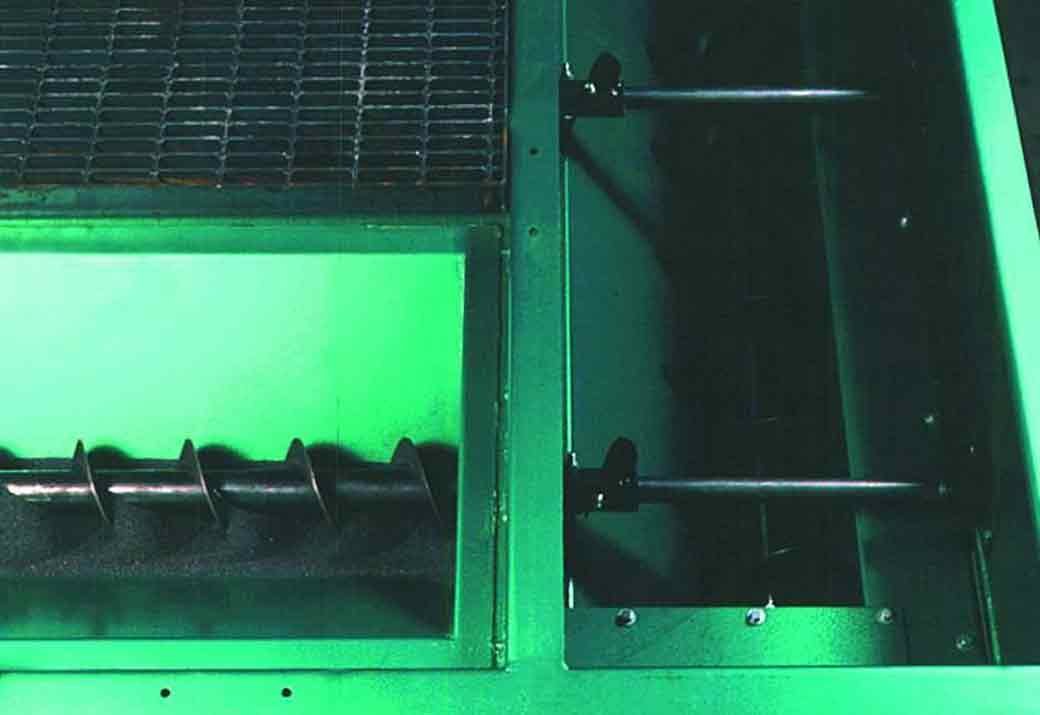
Screw Conveyor Recovery Floor

Scraper Conveyor Recovery Floor
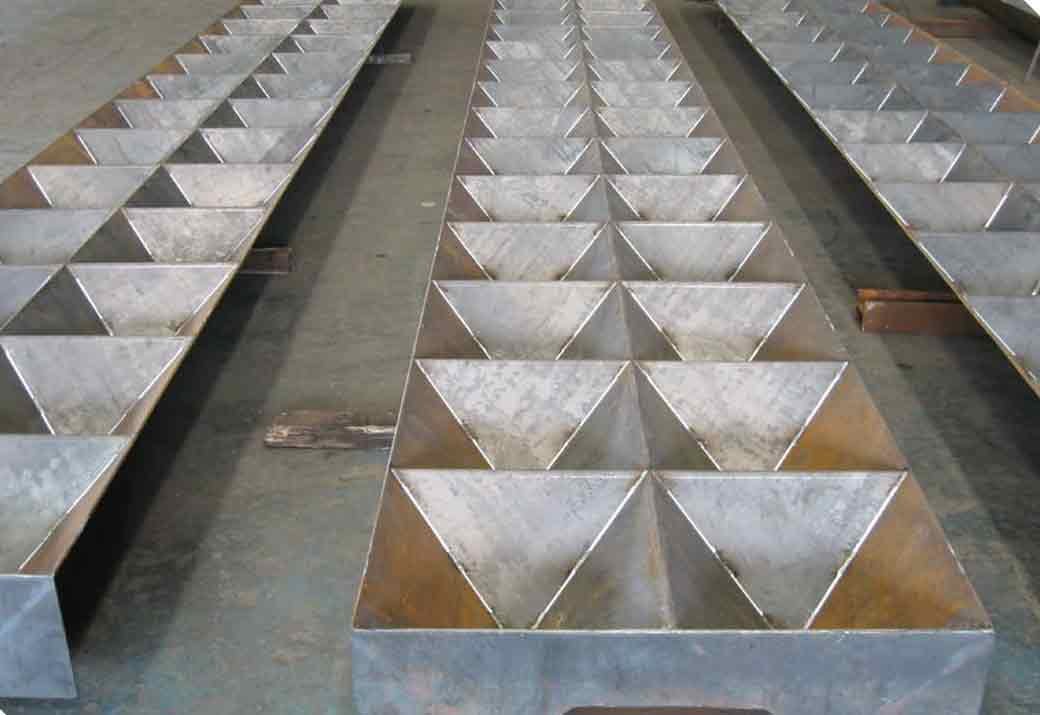
Pneumatic M Section Recovery Floor
In a 100% floor recovery system for abrasive blasting operations, the spent abrasive is efficiently collected as it descends through the floor grating. Various conveyor systems are commonly employed to transport the collected abrasive across the blast room to a designated area for further processing. These conveyor systems include pneumatic recovery systems, scraper conveyor recovery systems, screw conveyor recovery systems, and oscillating tray conveyors.
A. Pneumatic Recovery System:
Description: Pneumatic recovery systems use air flow to convey spent abrasive materials from the blast area to the collection and processing zone.
Advantages: They are known for their versatility, allowing for efficient transport of abrasive materials over short or long distances.
B. Scraper Conveyor Recovery System:
Description: Scraper conveyor recovery systems use a chain-driven mechanism with attached scrapers to move and collect the spent abrasive material.
Advantages: These systems are robust and effective, especially in handling heavier or bulkier abrasive materials.
C. Screw Conveyor Recovery System:
Description: Screw conveyor recovery systems utilize a rotating helical screw to move and lift the spent abrasive material for transportation.
Advantages: They are well-suited for applications where a continuous and gentle conveying motion is required.
D. Oscillating Tray Conveyor:
Description: Oscillating tray conveyors employ a back-and-forth oscillating motion to transport the spent abrasive across the blast room.
Advantages: Known for reliability, self-cleaning capabilities, low maintenance, and a low-profile design, making them suitable for efficient under-floor recovery requirements.
Following the transportation phase, the conveyor carries the spent abrasive to a bucket elevator, which lifts the material to a designated height. At this point, the abrasive is directed to an abrasive cleaning station where further processing occurs. This cleaning station
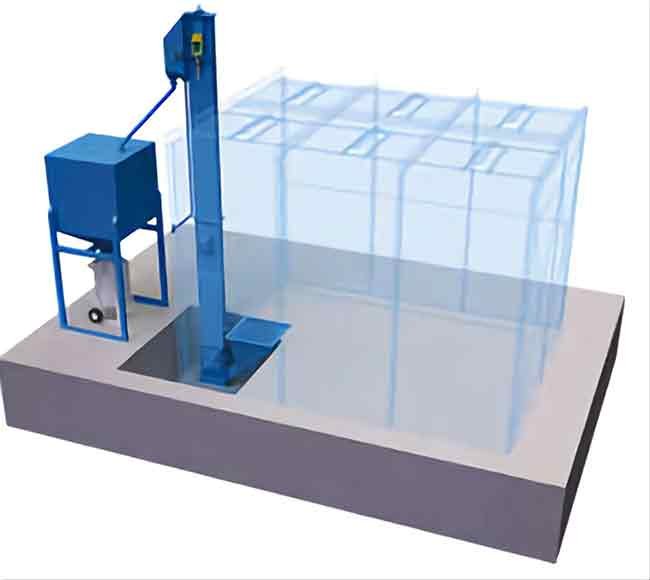
Sweep Chute Abrasive Recovery System
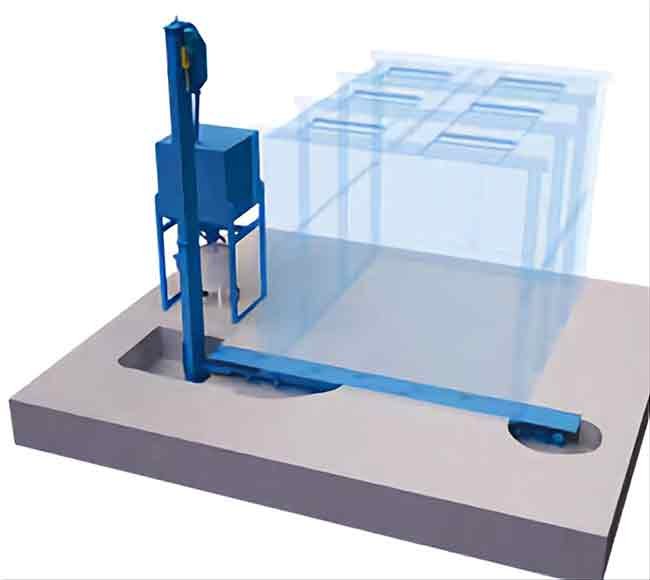
I Type Abrasive Recovery System
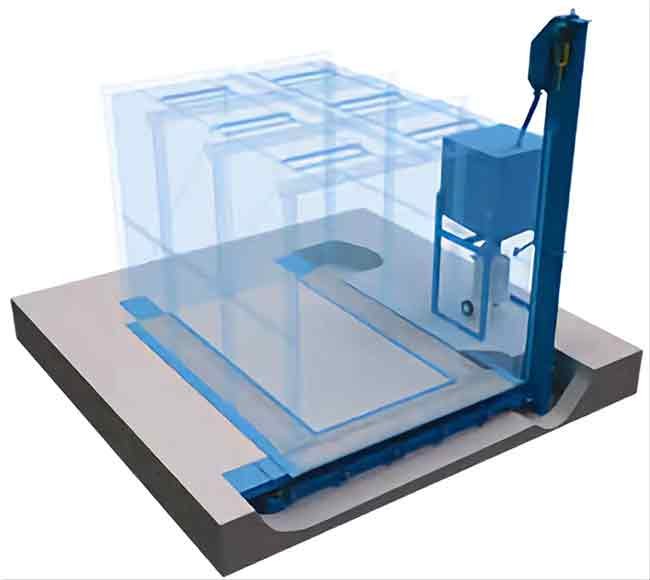
U Type Abrasive Recovery System
Oscillating tray conveyors are a reliable and self-cleaning solution for efficient under-floor recovery requirements. These conveyors are designed to require minimal maintenance and have a low profile, making them suitable for blast rooms with space constraints. The oscillating motion of the tray assists in the continuous and effective movement of abrasive material to the recovery system.
In summary, the choice of a recovery system in abrasive blasting operations is a critical decision that balances productivity, operator involvement, and maintenance requirements. A 100% floor recovery system, particularly with the use of oscillating tray conveyors, stands out as an efficient and low-maintenance solution that enhances overall operational efficiency.
Break Free from Constraints with Blasting Room
6. Blasting Room Dust Collectors
The performance of the dust collector is paramount in ensuring the efficiency of a blast cleaning operation. Incorrect design or malfunction can lead to severe consequences, impacting both the quality of the process and the overall working environment. The BlastKing HT type dust collectors are specifically engineered for the demanding conditions associated with blast cleaning operations, addressing and eliminating various issues that may arise if the dust collector is not up to par.
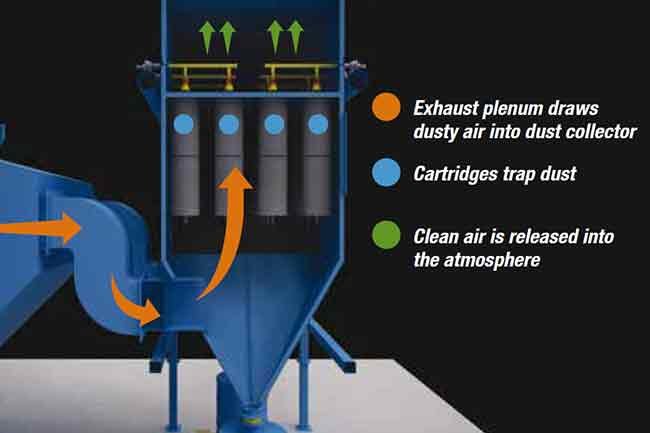
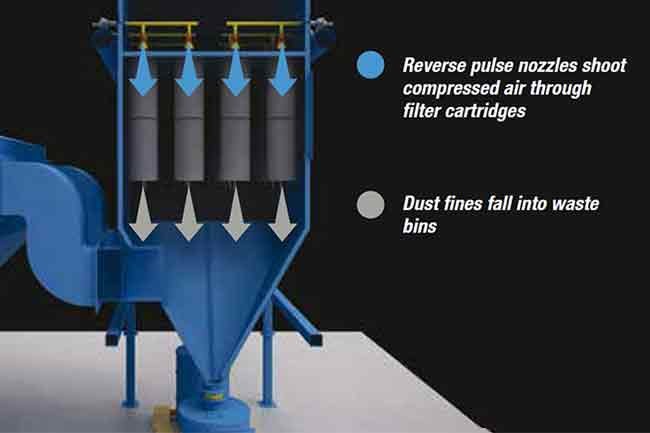
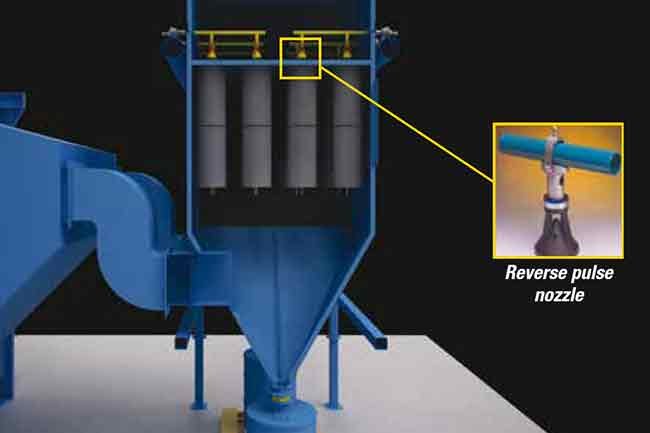
The BlastKing HT type dust collectors are tailored for the challenges of blast cleaning operations, ensuring:
Efficient Dust Collection:
Properly designed to effectively collect dust, maintaining a clean environment within the blast room.
Environmental Compliance:
Minimizing dust emissions, aligning with environmental regulations and responsible operational practices.
Upgrade Capability:
Available as an upgrade for existing blasting equipment fitted with inefficient, under-capacity, or poorly designed dust collectors.
In conclusion, the performance of the dust collector is integral to the success of a blast cleaning operation. The BlastKing HT type dust collector addresses potential issues, ensuring a cleaner, safer, and more environmentally friendly blasting environment.
Take the Leap into Infinite Innovation
Don’t let innovation pass you by. Seize the opportunity to transform your creative process with the Blasting Room. Join us on this journey towards infinite possibilities.
Call us today at +86 135 8931 7685
7. FAQs (Frequently Asked Questions)
8. Conclusion
In conclusion, the importance of blasting rooms in industrial processes is paramount. These controlled environments play a crucial role in enhancing the efficiency, safety, and precision of abrasive processes across diverse sectors. As technology advances, the capabilities of blasting rooms are expected to evolve, ensuring their continued indispensability in the industrial landscape.
It’s noteworthy that alongside traditional blasting rooms, more efficient solutions like dust free vacuum blasting machines and auto shot blasting machines for surface preparation have emerged. These machines offer enhanced efficiency and significant cost savings in terms of labor. They represent a technological advancement that complements or, in some cases, surpasses the capabilities of conventional blasting rooms. The continuous innovation in surface preparation technologies underscores the dynamic nature of the industrial sector, where optimizing processes is a constant pursuit for increased productivity and resource efficiency.