Concrete floor shot blasters are essential in surface preparation, enhancing floor durability in various settings, including industrial spaces, commercial establishments, and historical restoration projects. These machines, proven in transforming concrete surfaces, will be explored in terms of operational mechanisms, applications, safety protocols, and future trends.
I. Introduction
A. Definition of Concrete Floor Shot Blaster
Concrete floor shot blasters represent specialized machinery crafted for the preparation of concrete surfaces. They employ abrasive materials, such as high-velocity propelled steel shot or grit, to cleanse, profile, and etch the concrete. This procedure is pivotal in attaining ideal adhesion for coatings or overlays.
Effective surface preparation is a cornerstone for the success of any flooring project. Shot blasting not only removes contaminants and imperfections but also creates a profile that enhances the bonding of subsequent materials. This method has gained popularity for its efficiency and versatility in various applications.
Sustainability Redefined: Shot Blasting for a Greener Tomorrow
II. Advantages
The concrete floor shot blaster boasts a myriad of benefits, positioning it as the favored option for surface preparation.
A. Speed and Efficiency
A notable advantage lies in the rapid operation of shot blasting, significantly curtailing project timelines. This efficiency renders it a suitable choice for both expansive industrial endeavors and more compact residential refurbishments.
B. Environmentally Conscious Solutions
In contrast to conventional methods involving chemical stripping, shot blasting presents an eco-friendly alternative. By eliminating the necessity for harsh chemicals, it promotes a greener and more sustainable approach to surface preparation.
C. Cost-Effectiveness
Despite delivering impeccable results, concrete floor shot blasting surprisingly remains cost-effective. It diminishes labor expenses and alleviates the need for extensive surface repairs, emerging as a economical preference for property owners.
III. Technical Specification
Type | KBF200 | KBF270 | KBF550 | KBF800 | KBF1000 | KBF1200 |
---|---|---|---|---|---|---|
Blasting width (mm) | 200mm | 270 | 550 | 800 | 1000 | 1200 |
Travel speed (mm) | up to 20m/min | up to 23m/min | up to 26m/min | up to 26m/min | up to 26m/min | up to 26m/min |
Production capacity (m/min) | up to 50m2/h | up to 100m2/h | up to 450m2/h | up to 600m2h | up to 900m2h | up to 1100m2h |
blast motor power(Kw) | 7.5 | 7.5 | 2×11 | 2×15 | 2×18.5 | 2×22 |
Voltage | customized | customized | customized | customized | customized | customized |
Dust hose connection(mm) | ⌀150×20000 | ⌀150×20000 | ⌀200×20000 | ⌀200×20000 | ⌀200×20000 | ⌀200×20000 |
Dimensions | 1295 x 406 x 1193 | 1590 x 425x 1020 | 1956 x 711 x 1397 | 2286 x 1188x 1463 | 2200 x 1180x 1450 | 2450 x 1450x 1700 |
Weight | 160kgs | 200kgs | 595kgs | 770kgs | 1100kgs | 1300kgs |
Efficiency Meets Elegance: The Shot Blasting Advantage
Is downtime costing you money? Are traditional methods falling short on quality? Do you desire a solution that’s both swift and sophisticated?
Discover the seamless blend of efficiency and elegance with our concrete floor shot blaster. Elevate your space while minimizing downtime.
Call us today at +86 135 8931 7685
IV. Applications of Concrete Floor Shot Blasters
Commercial establishments, such as warehouses, retail spaces, and parking garages, benefit from the use of shot blasters to prepare surfaces for decorative coatings or polished concrete finishes.
Historical buildings often require delicate restoration work. Shot blasting proves invaluable in removing layers of old paint, restoring the original aesthetics without causing damage to the underlying structure.
In industrial settings, where floors endure heavy traffic and potential chemical exposure, shot blasting is a preferred method for surface preparation. It ensures a durable and resilient foundation for industrial flooring systems.
Commercial establishments, such as warehouses, retail spaces, and parking garages, benefit from the use of shot blasters to prepare surfaces for decorative coatings or polished concrete finishes.
Historical buildings often require delicate restoration work. Shot blasting proves invaluable in removing layers of old paint, restoring the original aesthetics without causing damage to the underlying structure.
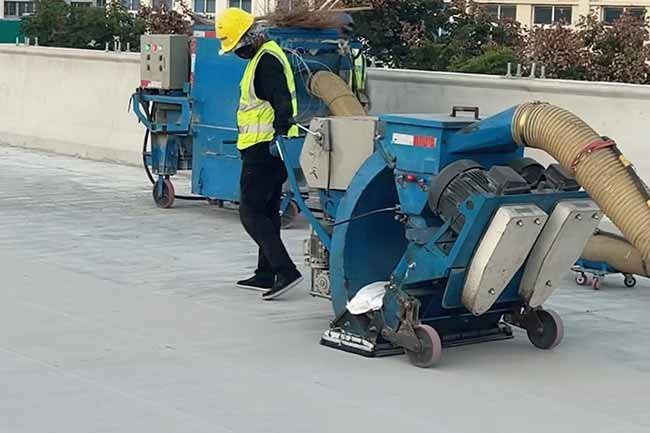
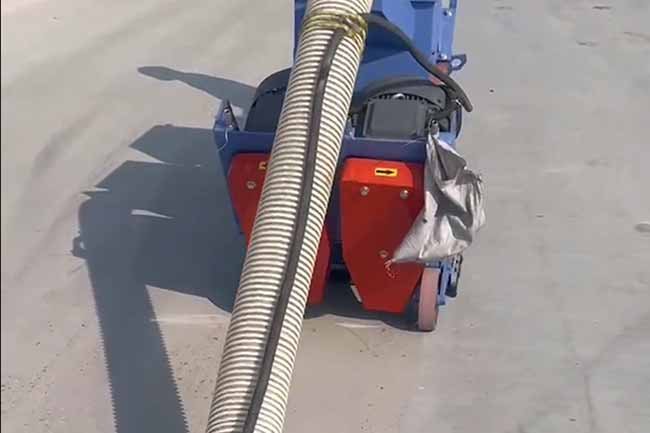
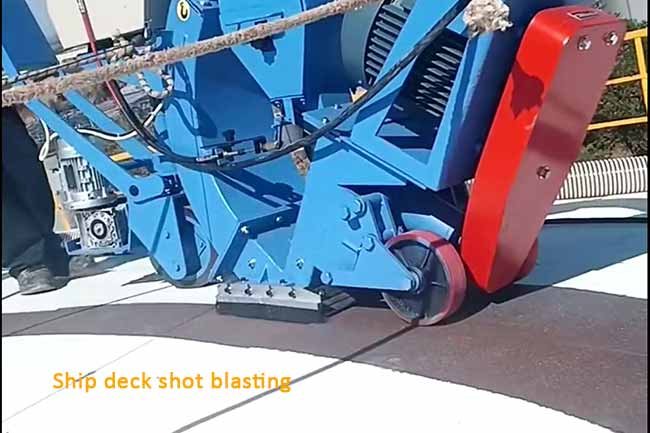
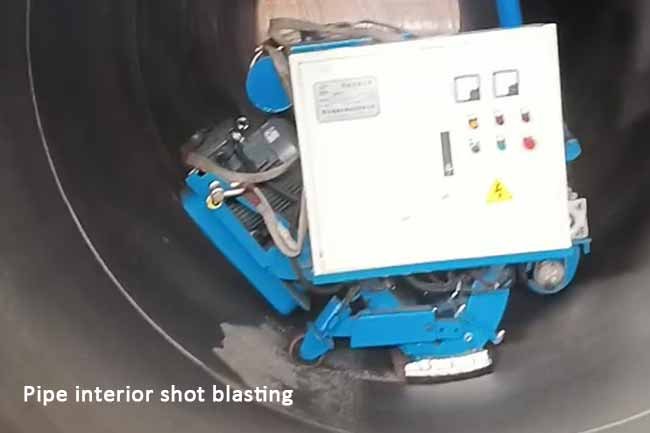
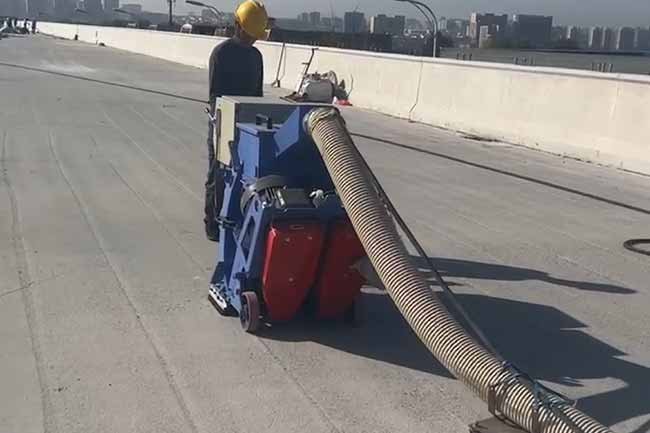
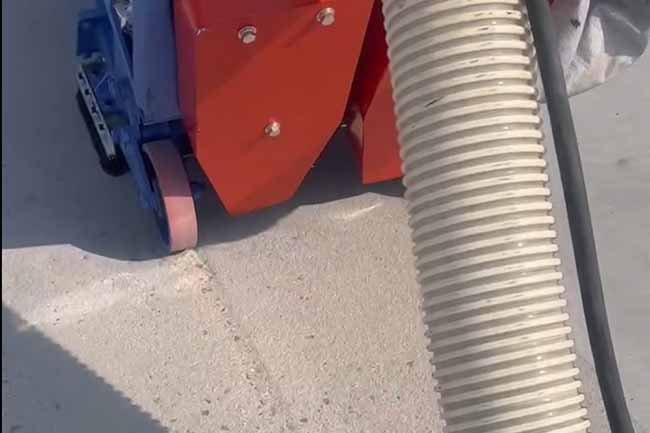
V. Choosing the Right Concrete Floor Shot Blaster
A. Project Size Consideration
The magnitude of the project plays a pivotal role in choosing the right shot blasting equipment. Centrifugal shot blasters are favored for expansive projects, while airless or wet shot blasting may be appropriate for more confined areas.
B. Surface Hardness and Condition
The concrete surface’s hardness and condition determine the choice of abrasive media and equipment. Shot blasting can be tailored to accommodate various hardness levels, ensuring optimal outcomes.
C. Dust Collection Systems
Effective dust control holds substantial importance, particularly in enclosed spaces or areas subject to stringent environmental regulations. Opting for shot blasting equipment equipped with efficient dust collection systems is paramount.
Sustainability Redefined: Shot Blasting for a Greener Tomorrow
VI. The Floor Shot Blaster for Ship Deck and Steel Plate Application
A self-propelled horizontal movable shot blaster designed for ship deck and steel plate applications is a specialized equipment used in surface preparation and cleaning processes. This powerful machine is engineered to efficiently blast abrasive material (such as steel shot) onto the surface of ship decks and steel plates to remove rust, old coatings, and contaminants. The mobility of the shot blaster allows it to cover large areas with ease, ensuring thorough and uniform surface preparation.
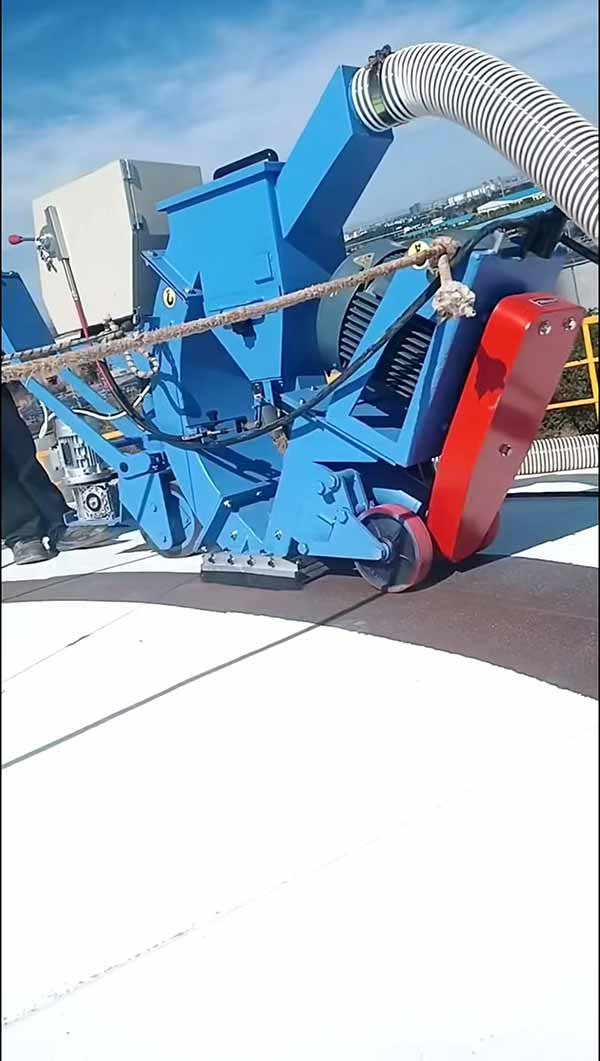
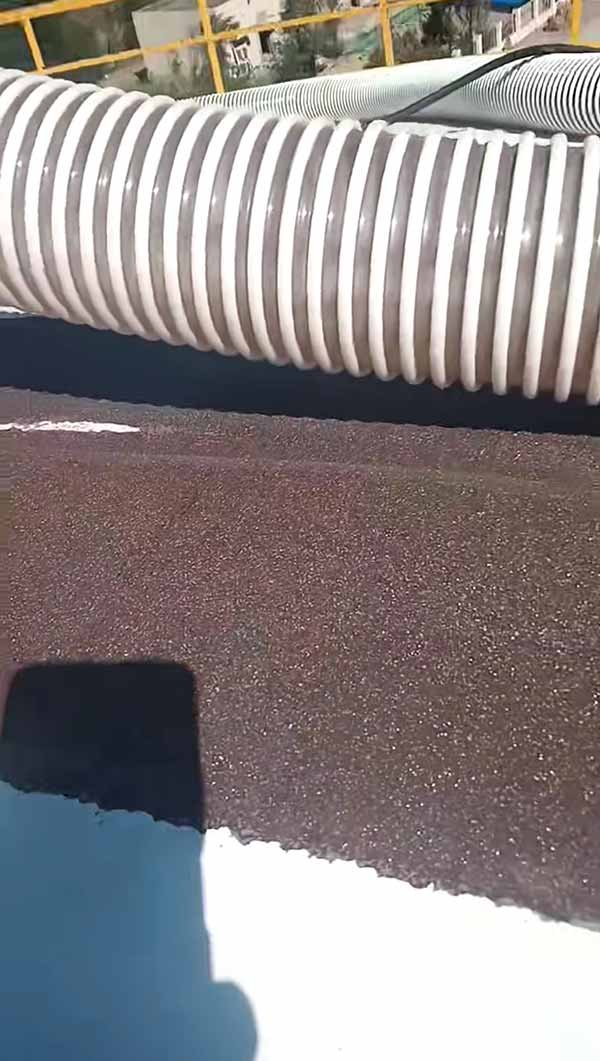
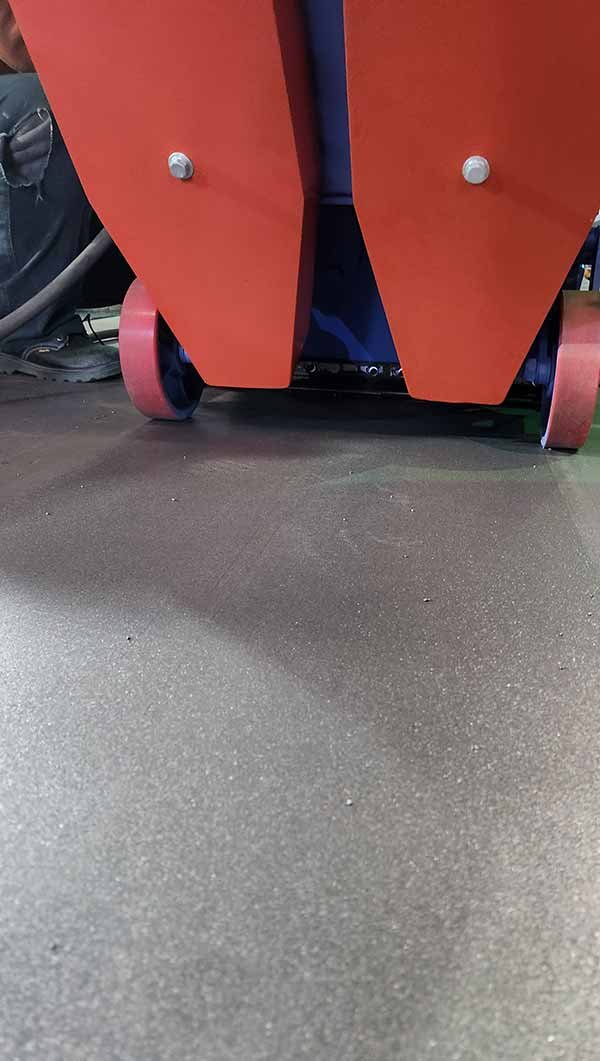
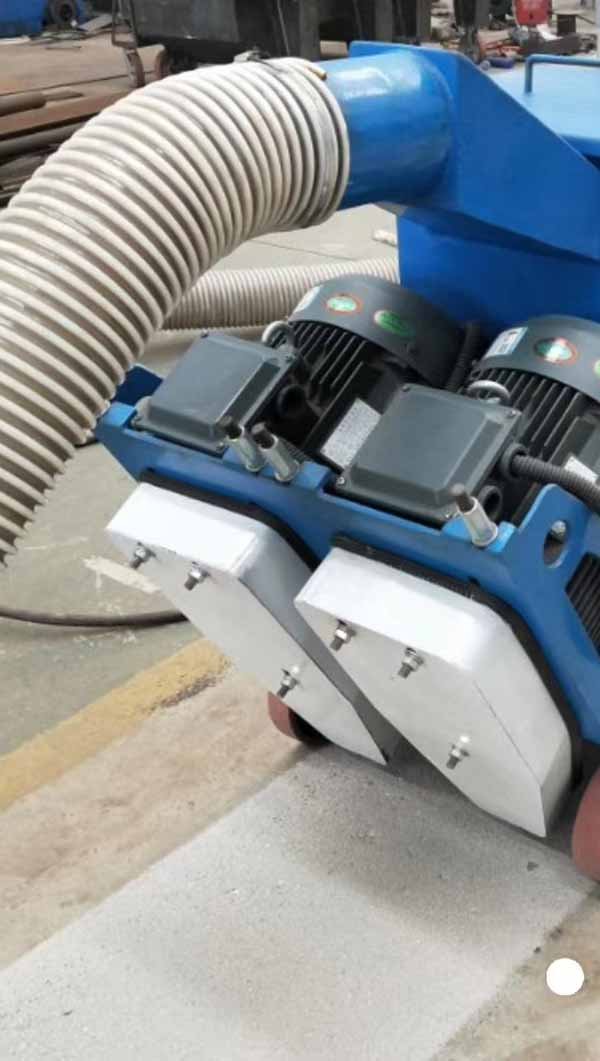
1. Self-Propelled Design:
The shot blaster is equipped with a self-propulsion system, allowing it to move horizontally across the ship deck or steel plate. This feature enhances efficiency and reduces the need for manual labor in moving the equipment.
2. Adjustable Blasting Parameters:
The machine is designed to offer flexibility in adjusting blasting parameters such as blast pressure, abrasive flow rate, and nozzle angle. This adaptability ensures optimal performance on different surfaces and under varying conditions.
3. Dust Collection System:
To maintain a clean and safe working environment, the shot blaster is often equipped with an efficient dust collection system. This system captures and contains the dust generated during the blasting process, preventing it from dispersing into the surrounding area.
4. Robust Construction:
Given the demanding nature of ship deck and steel plate applications, the shot blaster is constructed with durable materials to withstand harsh conditions and heavy usage. This ensures a longer operational life and reduced maintenance requirements.
5. Operator Safety Features:
Safety is a top priority, and these machines typically come with features such as emergency stop buttons, protective barriers, and user-friendly controls to enhance the safety of the operators.
6. Versatility:
The shot blaster is designed to handle various surface profiles and substrate conditions. It can effectively remove corrosion, paint, and other surface contaminants, preparing the surface for coatings or repairs.
7. Ease of Maintenance:
The design often incorporates features that make maintenance tasks straightforward, including easy access to critical components and quick-change systems for consumables like blast media and nozzles.
In summary, a self-propelled horizontal movable shot blaster for ship deck and steel plate applications is a sophisticated piece of equipment designed for efficiency, versatility, and safety in the preparation of surfaces for maintenance or coating processes in maritime and industrial settings.
Protect Your Concrete Investments, Avoid Costly Repairs!
💰 Concerned about frequent repairs eating into your budget for concrete structures? Our shot blasting solutions safeguard your investments, reducing maintenance costs significantly.
Call us today at +86 135 8931 7685
VII. Maintenance Tips for Horizontal Movable Floor Shot Blasters
To ensure optimal performance and longevity of a self-propelled horizontal movable shot blaster, adhering to essential maintenance practices is crucial. Here are key tips to keep your equipment in top condition:
1. Regular Inspections:
Conduct routine inspections, checking for visible wear, loose components, or damage. Pay close attention to critical elements like the blast wheel, blades, and wear plates.
2. Lubrication and Cleaning:
Implement a regular lubrication schedule for all moving parts, including bearings and chains. Thoroughly clean the equipment after each use to eliminate abrasive residues and prevent debris buildup.
3. Blast Wheel Maintenance:
Regularly inspect the blast wheel for wear and tear. Ensure blades are in good condition and correctly aligned. Promptly replace any damaged or worn components.
4. Dust Collection System:
If equipped, ensure the dust collection system functions effectively. Clean or replace filters as needed to maintain proper dust containment during operation.
5. Check Electrical Components:
Inspect all electrical components, such as wiring, switches, and control panels. Look for signs of damage or wear. Keep electrical connections clean and tight to prevent malfunctions.
6. Tracking and Alignment:
Regularly check the tracking and alignment of the shot blaster. Misalignment can lead to uneven surface preparation. Adjust tracking as necessary to maintain accuracy during operation.
7. Replace Consumable Parts:
Keep an inventory of consumable parts like blades, wear plates, and seals. Replace these parts at recommended intervals to ensure consistent performance and avoid unexpected breakdowns.
8. Inspect Safety Features:
Verify that all safety features, including emergency stop buttons and safety interlocks, are in proper working condition. Regularly test these features to ensure effectiveness in case of an emergency.
9. Training for Operators:
Ensure operators are well-trained in the proper use and maintenance of the shot blaster. Provide refresher courses to keep them updated on safety protocols and equipment handling.
10. Record Keeping:
Maintain a comprehensive record of maintenance activities, including inspection dates, repairs, and parts replacements. This documentation aids in tracking the overall health of the shot blaster and planning future maintenance tasks.
11. Professional Servicing:
Schedule regular professional servicing by qualified technicians. Professionals can identify potential issues, conduct in-depth inspections, and provide specialized maintenance to ensure the longevity of your shot blaster.
By following these maintenance tips, you can extend the life of your self-propelled horizontal movable shot blaster, ensuring consistent, high-quality performance in concrete surface preparation and other applications.
Unlock Potential, Embrace Possibilities: The Shot Blasting Experience
VIII. FAQs (Frequently Asked Questions)
IX. Conclusion
A. Recap of Key Points
Concrete floor shot blasters present a revolutionary solution for surface preparation, delivering advantages like improved adhesion, contaminant removal, and surface profiling. The wide-ranging applications, adherence to safety measures, and exploration of future trends emphasize the pivotal role of shot blasting in the flooring industry.
B. Future of Concrete Floor Shot Blasters
In the trajectory of technological evolution, concrete floor shot blasters anticipate further advancements, encompassing heightened automation, sustainability initiatives, and integration with intelligent systems. These innovations are poised to enhance the efficiency and environmental consciousness of surface preparation processes.
We deliver results