Key Benefits for Shot Blasting and Priming Machine
- Continuous blasting and coating
- Highly performance ORICA blast turbines
- Versatile transport technology
- High process security
Features for Preservation Line
- Complete systems quoted
- One supplier for all components
- Proven abilities – Industry leader
- Quality components
- Proven technology
- Custom designs – Flexible layouts
- Simple integration into existing manufacturing processes
- Wide range of system sizes and variants
Application
Preservation lines are used for pre- and final coating.
The main area of application is coating parts with a welding primer for temporary corrosion protection.
A shot blasting and priming machine usually consists of specially engineered conveyor systems, a roller conveyor shot blast machine, a pre-heater, an automatic paint spray system and a subsequent dryer. Depending on the customer requirements, different types of conveyor systems may be used, such as roller conveyors, chain or slat conveyors, cross conveyors, etc. The entire line is totally engineered around the specific application and size and geometry of the parts.
Shot Blasting and Priming Machine
Shot Blasting and Priming Machine combine the heating (drying), blasting, coating and drying of workpieces such as sheet steel, profiles, pipes or steel structures in one automatic line.
The shot blasting and priming machines are ideal when there is a lengthy manufacturing or storage time between blasting and final coating. In order to prevent rust returning, a weld primer is applied to provide corrosion resistance for weeks.
Sheet widths of up to 5000mm can be processed, with passage speeds varying from 1.0m/min to 5.0m/min.
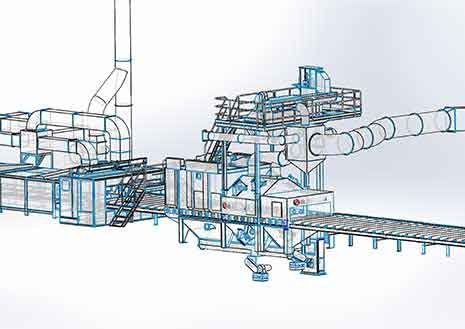
The roller conveyor shot blast systems are an essential part of the overall preservation line. The parts (large steel sheets, tubes and round bars, angle bars and I-beams) travel on a roller conveyor through the pre-heater chamber, the blast chamber and a blow-off/brush-off station. The high performance blast wheels – mounted to the machine housing – ensure all-round and reproducible blast coverage of the parts, while providing an optimal preparation of the parts surface for the subsequent primer coating.
Shot Blasting Cabinet and Abrasive Removal Unit
As with all BlastKing roller conveyors Blast Machines the shot blasting cabinet liner is manufactured completely from high manganese. High manganese has a property which is hard enough to deal with the shot blasting from 35HRC to more than 60HRC. They are attached from the outside and are easy to replace. When aggressive shot is used, additional lining of high manganese, tool steel or cast material can be provided.To avoid shot leakage, several rubber layers or curtains are fitted in areas of heavy wear. These are mounted in a V-Track and are easy to replace.After the blasting process, the workpiece may still be in blast media, which must be cleaned off. This task is carried out by a rotating brush and a high blow off station. The brush is fitted with securely attached brush segments, which are interchangeable.To avoid blast media building up on long parts, the rotation brushes remove the spent abrasive from the workpieces surface into a specially designed trough which has a screw conveyor taking the media back into circulation. To keep the position between the brushes and the screw conveyor constant when blasting different sized work pieces, both are built with the same adjustable framework. Finally any remaining media on the work pieces will be removed by the blow off station, which is mounted on the same framework and uses high pressure ventilators to blow off any media remaining.
Cartridge Filter Unit
Each BlastKing machine is equipped with multiple cartridge filters. These filters are necessary to remove any impurities from the air used to blast resulting in a more even, direct, and effective blast.Benefits experienced with the BlastKing’ cartridge filters:
Large distance between folds in each cartridge filter leads to precise cleaning and better air pressure.
The impact separator within the cartridge filter unit ensures that the broken down fines are separated (which protects the filter cartridge against unnecessary wear).
The cartridge filters clean the cartridge automatically using an air pressure pulse, the intensity and duration of the pulse can be adjusted according to the type and amount of dust.
Pressure difference is monitored to automatically set the cleaning cycle increasing the life time of the cartridge and saves compressed air.
Easy exchange of cartridge filters.
Correct contact pressure.
Low compressed air consumption.
Constant cleaning, from top to bottom, due to conical design of the cartridge filter.
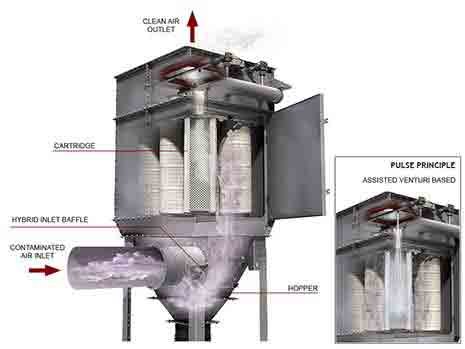
BlastKing ORICA Wheel
BlastKing group have the patented technology of the direct drive blasting turbine which motor power from 22kw to 75kw.
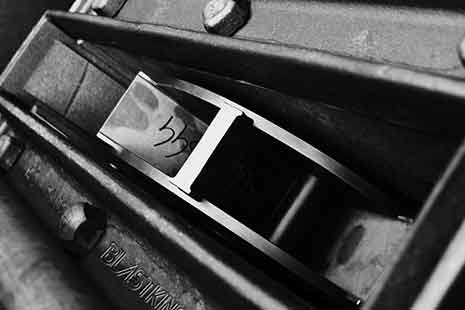
References to Shot Blasting and Priming Machine
Installation, Post-sales, Training & Safety
BlastKing Provide turnkey installation for the shot blaster. DIY installation by customer is also available according to the comprehensive documents, videos and drawings which provide by BlastKing, our engieers team also can provide real-time installation guidance.
The successful implementation of any blasting equipment is based upon the total commitment and dedication to the process. BlastKing’s field technicians are involved in the installation and training of the programmer and operator at the customer’s site or at BlastKing’s training facility. BlastKing has developed a complete program of maintenance training seminars. These are scheduled not only for new users but also for existing users. This structure is ideal for customers to send new employees so they can become more conversant with all BlastKing’s equipment.
Guarantee time of shot blasting machine will be one to five years. Technical support will be during the whole blasting machine life. Consumable spare parts will be supplied periodically.
All the equipment from BlastKing is conformity with CE&BV standard, and our factory have ISO9001, ISO14001 certification.
General emergency stop button is on all the BlastKing’s control panel. And sub emergency stop buttons are on conveyor systems. Detectors on the blast wheel covers, blasting chamber windows, elevators, separators will protect safety of the operators. Dust collection unit of shot blast machine dust emisssions is under 3mg/m3 which also bring dust free working environment.