Surface cleaning has undergone a remarkable transformation in recent years, thanks to the advent of wet blasting machine technology. This innovative method has revolutionized the way we approach tasks ranging from industrial cleaning to historical restoration. In this article, we will delve into the intricacies of wet blasting, exploring its working principles, advantages, applications, and much more.
I. Introduction
A. Definition and Purpose of Wet Blasting Machine
The Wet Blasting Machine is an innovative cleaning tool that utilizes a combination of water and abrasive materials to remove contaminants and coatings from various substrates. Unlike traditional dry blasting methods, wet blasting significantly reduces dust emissions, offering a cleaner and more environmentally friendly solution.
B. Importance of Efficient Surface Cleaning
Efficient surface cleaning is crucial across multiple industries. Whether preparing surfaces for painting, maintaining industrial equipment, or restoring historical structures, the quality of the cleaning process directly impacts the outcome of subsequent tasks.
II. Evolution of Surface Cleaning
A. Traditional Methods and Their Limitations
Traditional surface cleaning methods, such as dry blasting, often come with inherent challenges. The release of dust into the air poses health risks, while the abrasive nature of these methods can cause damage to delicate surfaces.
B. Emergence of Wet Blasting Technology
The need for a safer and more precise alternative gave rise to wet blasting technology. By combining water with abrasive media, this method minimizes dust production and provides a gentler yet effective cleaning process.
III. How Wet Blasting Works
A. Components of a Wet Blasting Machine
A typical wet blasting machine comprises a few key components: a blasting cabinet, a pump system, an abrasive storage hopper, and a control panel. These elements work in harmony to deliver a controlled and efficient cleaning process.
B. The Science Behind Wet Abrasive Media
The effectiveness of wet blasting lies in the synergy between water and abrasive media. The water acts as a lubricant, reducing friction and heat generated during the cleaning process. This not only enhances precision but also prolongs the life of the abrasive media.
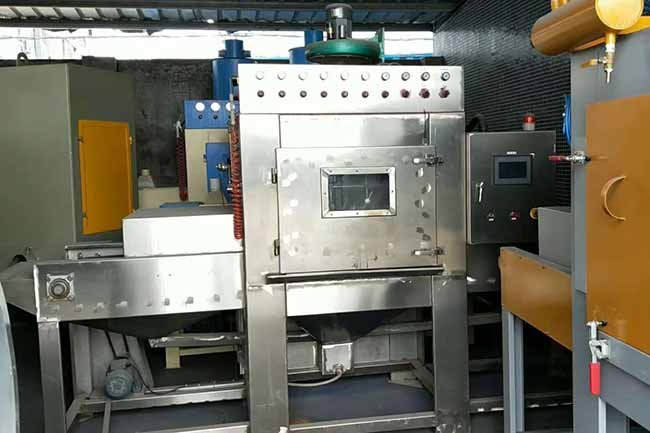
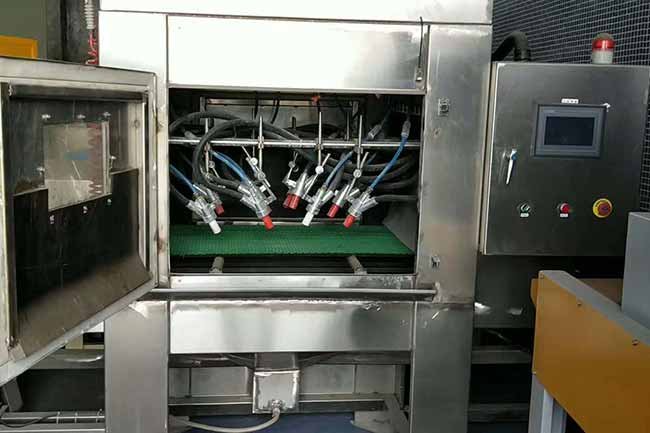
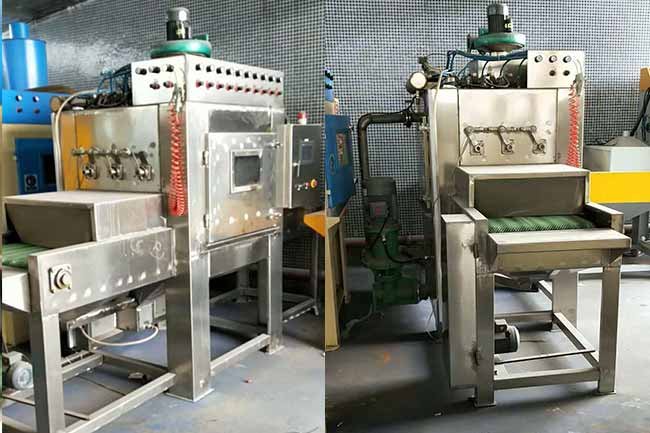
IV. Advantages of Wet Blasting
A. Reduced Dust and Environmental Impact
One of the standout features of wet blasting is its ability to minimize dust emissions significantly. This not only creates a healthier working environment but also aligns with increasingly stringent environmental regulations.
B. Enhanced Precision in Surface Preparation
Wet blasting allows for precise control over the cleaning process. Operators can adjust parameters such as water pressure, abrasive flow rate, and nozzle distance, ensuring optimal results without damaging the substrate.
C. Versatility in Substrate Compatibility
Unlike some dry blasting methods that may be too abrasive for certain materials, wet blasting is versatile and can be employed on a wide range of substrates, including metals, composites, and delicate surfaces.
The effectiveness of wet blasting lies in the synergy between water and abrasive media. The water acts as a lubricant, reducing friction and heat generated during the cleaning process. This not only enhances precision but also prolongs the life of the abrasive media.
We are manufacturer since 1982
V. Applications of Wet Blasting
A. Industrial Cleaning and Maintenance
Industries such as manufacturing, oil and gas, and power generation benefit from wet blasting in equipment maintenance. The method’s ability to remove contaminants without causing damage makes it a preferred choice for preserving machinery.
B. Restoration of Historical Structures
Historical structures, often delicate and intricately designed, require a gentle yet effective cleaning method. Wet blasting proves invaluable in restoring these architectural marvels to their former glory without compromising their integrity.
C. Automotive and Aerospace Industries
In sectors where precision is paramount, such as automotive and aerospace, wet blasting ensures thorough cleaning without the risk of surface damage. This is particularly crucial for components like engine parts and aircraft surfaces.
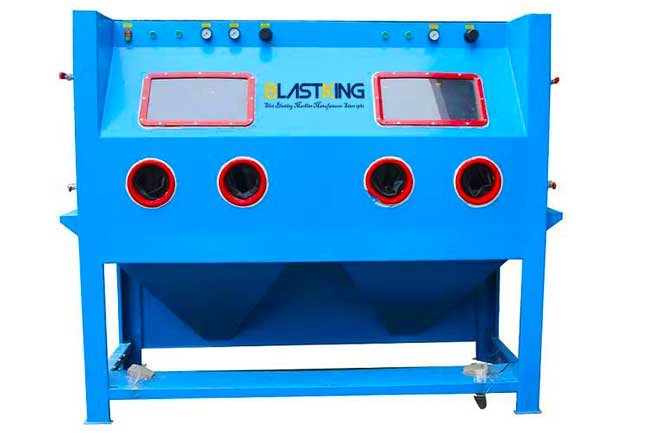
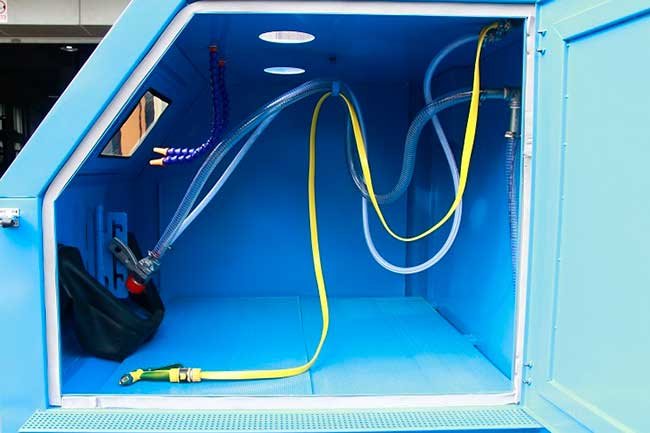
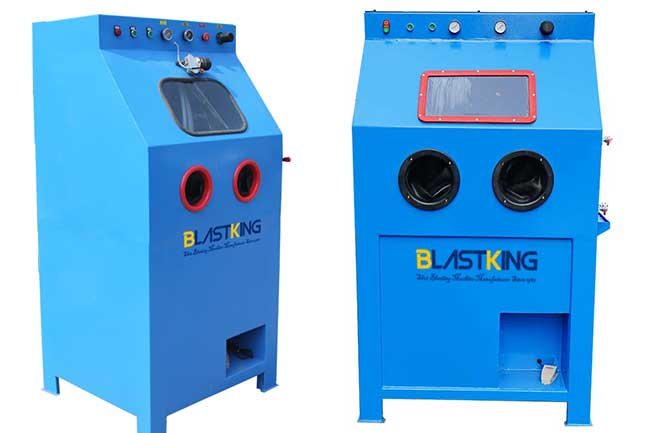
VI. Choosing the Right Abrasive Media
A. Understanding Different Abrasives
Selecting the appropriate abrasive media is a critical aspect of wet blasting. Factors such as hardness, size, and composition influence the cleaning efficiency and the impact on the substrate.
B. Factors Influencing Media Selection
The nature of the cleaning task, the type of substrate, and the desired surface finish all play a role in determining the ideal abrasive media. Operators must consider these factors to achieve optimal results.
VII. Common Mistakes to Avoid
A. Inadequate Safety Measures
While wet blasting is generally safer than dry blasting, neglecting safety measures can still lead to accidents. Operators must use personal protective equipment and follow proper procedures to mitigate risks.
B. Improper Equipment Maintenance
Regular maintenance of wet blasting equipment is essential for sustained performance. Neglecting upkeep can result in decreased efficiency and potentially costly repairs.
We are manufacturer since 1982
VIII. Wet Blasting vs. Other Surface Cleaning Methods
A. A Comparative Analysis
Comparing wet blasting with other surface cleaning methods, such as dry blasting and chemical cleaning, provides insights into the advantages and limitations of each approach.
B. Cost-Effectiveness and Efficiency
Beyond its cleaning efficacy, wet blasting proves to be cost-effective in the long run. Reduced abrasive consumption and lower disposal costs contribute to its economic appeal.
IX. Real-World Success Stories
A. Case Studies Demonstrating the Effectiveness of Wet Blasting
Examining real-world applications through case studies showcases the tangible benefits of wet blasting in diverse industries. Success stories provide valuable insights for potential adopters.
B. Testimonials from Industries Benefiting from This Technology
Feedback from industries that have embraced wet blasting further validates its effectiveness. Testimonials highlight the positive impact on productivity, efficiency, and overall operational success.
X. Future Trends in Wet Blasting Technology
A. Innovations and Advancements
Ongoing research and development in wet blasting technology continue to yield innovations. From automated systems to improved abrasive recycling, the future holds exciting possibilities.
B. Potential Areas for Further Development
Identifying areas where wet blasting can further excel, such as increased automation and integration with smart technologies, points to the continuous evolution of this cleaning method.
XI. Tips for Optimal Wet Blasting Results
A. Best Practices for Operators
Providing practical tips for operators, including proper nozzle positioning, monitoring abrasive flow, and adjusting water pressure, ensures optimal results and prolongs equipment lifespan.
B. Maximizing Efficiency and Minimizing Downtime
Efficiency is key in any industrial process. Tips on streamlining wet blasting operations help businesses maximize productivity while minimizing downtime.
We are manufacturer since 1982
XII. Industry Regulations and Compliance
A. Environmental Regulations
Understanding and adhering to environmental regulations is vital for businesses utilizing wet blasting. Compliance ensures sustainable practices and avoids potential legal consequences.
B. Safety Standards for Wet Blasting
Ensuring the safety of operators and bystanders involves following established safety standards. Implementing training programs and regular equipment inspections contribute to a secure working environment.
XIII. DIY Wet Blasting: Pros and Cons
A. Overview of DIY Wet Blasting Kits
For individuals considering DIY wet blasting, an overview of available kits and their components helps in making informed decisions.
B. Precautions for Amateurs
DIY wet blasting comes with its own set of risks. Informing amateurs about potential hazards and the importance of safety precautions is essential for injury prevention.
XIV. Maintenance of Wet Blasting Equipment
A. Regular Checks and Troubleshooting
Routine checks and timely troubleshooting are essential for maintaining the optimal performance of wet blasting equipment. A well-maintained system ensures consistent and reliable results.
B. Extending the Lifespan of Your Wet Blasting Machine
Tips on preventive maintenance and proper storage contribute to extending the lifespan of wet blasting equipment, safeguarding the investment made by businesses.
XV. Conclusion
A. Recap of the Benefits of Wet Blasting
In conclusion, wet blasting stands out as a revolutionary method for surface cleaning, offering numerous advantages such as reduced dust, enhanced precision, and versatile applications across industries.
B. Encouraging the Adoption of This Revolutionary Cleaning Method
Encouraging businesses to embrace wet blasting is not just about adopting a cleaning method; it’s about investing in efficiency, safety, and environmental responsibility. The benefits far outweigh the initial transition challenges.
We are manufacturer since 1982