Benefits and Features
Key Benefits and Features for Barrel Shot Blasting Machines
5/8 thick manganese steel, solid welded drum (zero catch points, no sharp edges to nick or damage parts)
Replaceable actuator cone (different shapes for different part types )
Adjustable drum angles with shock loading suspension (easily modify tumbling dynamics)
5 point drum support (Better stability- durability)
Abrasion Resistant (AR) screws (longer life)
Machine can be fully automated (higher productivity)
Leak resistant piece door (maintenance advantages)
Applications
- Automotive
- Iron, steel and metal foundries
- Heat treat operations
- Forging operations
- Small stamping parts manufacturers
Barrel Shot Blasting Machines
The BlastKing Barrel Shot Blasting Machines are the ideal solution to clean parts that would normally become pinched or jammed in our traditional Tumblast machine, reducing chances of part damage. Barrel machines are designed for easy maintenance to provide shorter downtime. Barrel Machines adopt cost-effective and space-saving rotating drum systems. Versatile, solid manganese drums allow efficient tumbling of parts with no pinch points.
Typical uses for system includes the removal of sand, scale, rust and other contaminants from forged, heat treat and cast parts.
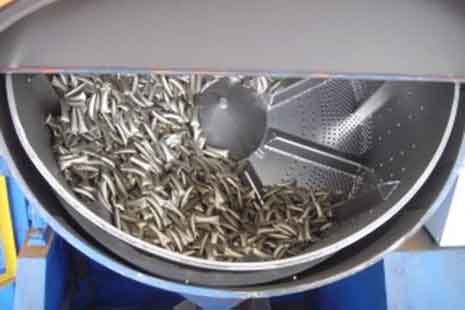
Available options of Barrel Type Shot Blasting Machines
- ORICA wheels with full lining package
- Abrasive Resistant elevator casing with replaceable endwalls in boot section
- Enhanced separators available
- Foundry duty magnetic separator
- Double lip airwash separator
- Automatic abrasive adder
Shot Blasting Cabinet
The blasting chamber is fabricated by high strengthened steel plates and profile steel which ensures adequate intensity and rigidity of the machine. ,blast wheels layout adopt 3-D dynamic simulation design, which ensures optimal shot blasting angle and distance.
As with all BlastKing Blast Machines adopt easy replaceable high manganese steel guard liner on hot blasting zone, which is hard enough to deal with the shot blasting hardness up to 60HRC. The overlapped liner blocks are installed inside the blasting chamber which eliminate any possibility that the high speed blasting media will hit the blasting chamber directly.
High impact toughness can make full use of the reflection kinetic energy of shot to continue to blast cleaning the surface of work piece, so greatly enhance the cleaning efficiency and quality.
High chrome wear resistant perforated saddle plate are deployed at the bottom of the blasting chamber which ensure the used blasting media will appropriately get into the abrasive recycle system and prevent any damages to the bottom screw conveyor.
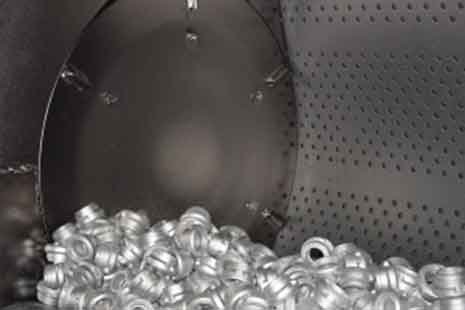
Cartridge Filter Unit
Each BlastKing machine is equipped with multiple cartridge filters. These filters are necessary to remove any impurities from the air used to blast resulting in a more even, direct, and effective blast.Benefits experienced with the BlastKing’ cartridge filters:
Large distance between folds in each cartridge filter leads to precise cleaning and better air pressure.
The impact separator within the cartridge filter unit ensures that the broken down fines are separated (which protects the filter cartridge against unnecessary wear).
The cartridge filters clean the cartridge automatically using an air pressure pulse, the intensity and duration of the pulse can be adjusted according to the type and amount of dust.
Pressure difference is monitored to automatically set the cleaning cycle increasing the life time of the cartridge and saves compressed air.
Easy exchange of cartridge filters.
Correct contact pressure.
Low compressed air consumption.
Constant cleaning, from top to bottom, due to conical design of the cartridge filter.
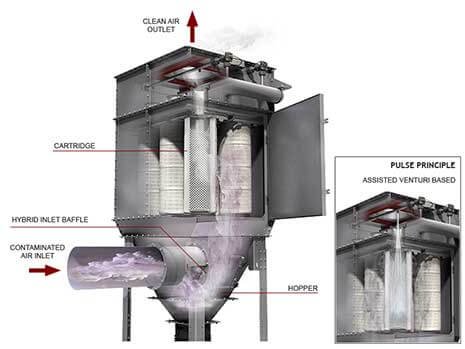
BlastKing ORICA Wheel
BlastKing group have the patented technology of the direct drive blasting turbine which motor power from 7.5kw to 75kw.
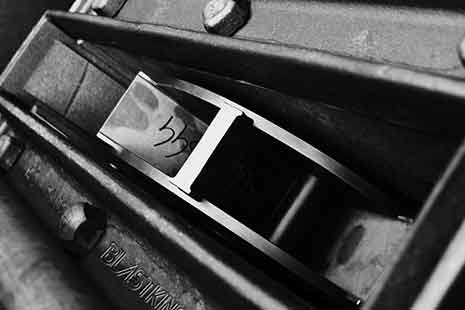
References to Barrel Shot Blasting Machines
Installation, Post-sales, Training & Safety
BlastKing Provide turnkey installation for the shot blaster. DIY installation by customer is also available according to the comprehensive documents, videos and drawings which provide by BlastKing, our engieers team also can provide real-time installation guidance.
The successful implementation of any blasting equipment is based upon the total commitment and dedication to the process. BlastKing’s field technicians are involved in the installation and training of the programmer and operator at the customer’s site or at BlastKing’s training facility. BlastKing has developed a complete program of maintenance training seminars. These are scheduled not only for new users but also for existing users. This structure is ideal for customers to send new employees so they can become more conversant with all BlastKing’s equipment.
Guarantee time of shot blasting machine will be one to five years. Technical support will be during the whole blasting machine life. Consumable spare parts will be supplied periodically.
All the equipment from BlastKing is conformity with CE&BV standard, and our factory have ISO9001, ISO14001 certification.
General emergency stop button is on all the BlastKing’s control panel. And sub emergency stop buttons are on conveyor systems. Detectors on the blast wheel covers, blasting chamber windows, elevators, separators will protect safety of the operators. Dust collection unit of shot blast machine dust emisssions is under 3mg/m3 which also bring dust free working environment.