Introduction
Ever looked at a batch of freshly cast or forged parts and thought, “These definitely need some TLC before they go anywhere near my customers”? You’re not alone. Every manufacturer faces the same challenge: rust, burrs, scale, and surface imperfections that simply can’t stay. That’s where BlastKing’s tumble shot blasting machines swoop in to save the day—like the superhero your production line didn’t know it needed.
We’ve been perfecting tumble belt shot blasting machines since 1982, and trust us, this isn’t just another piece of equipment. It’s your secret weapon for cleaner parts, lower costs, and a whole lot fewer headaches.
What Exactly Is a Tumble Shot Blasting Machine?
Imagine tossing your parts into a rotating drum while powerful blast wheels fire abrasive media at every angle. As the belt keeps things tumbling, each surface—inside, outside, curved, or flat—gets equal attention.
By the time the cycle ends, those components emerge looking brand new, ready for coating, assembly, or the open road. Whether you’re in automotive, aerospace, forging, or foundries, our tumble shot blast machines deliver consistency batch after batch.
The Power of Surface Prep: How Shot Blasting Transforms Results
Why Manufacturers Swear by BlastKing Tumble Blasters
Sure, lots of companies sell shot blasting equipment. But here’s what makes BlastKing the industry favorite:
-
Cleaner Parts, Less Effort: The tumbling motion does the heavy lifting, so every surface gets blasted evenly.
-
Compact Footprint: Big results without hogging factory floor space.
-
Budget-Friendly Operation: Lower abrasive use, reduced energy costs, and long-lasting components keep your expenses under control.
-
Material Versatility: Steel, aluminum, iron, or specialty alloys—it handles them all like a pro.
-
Built to Outlast Your Workload: Durable designs mean less downtime, more production time.
The bottom line? Better results with fewer headaches.
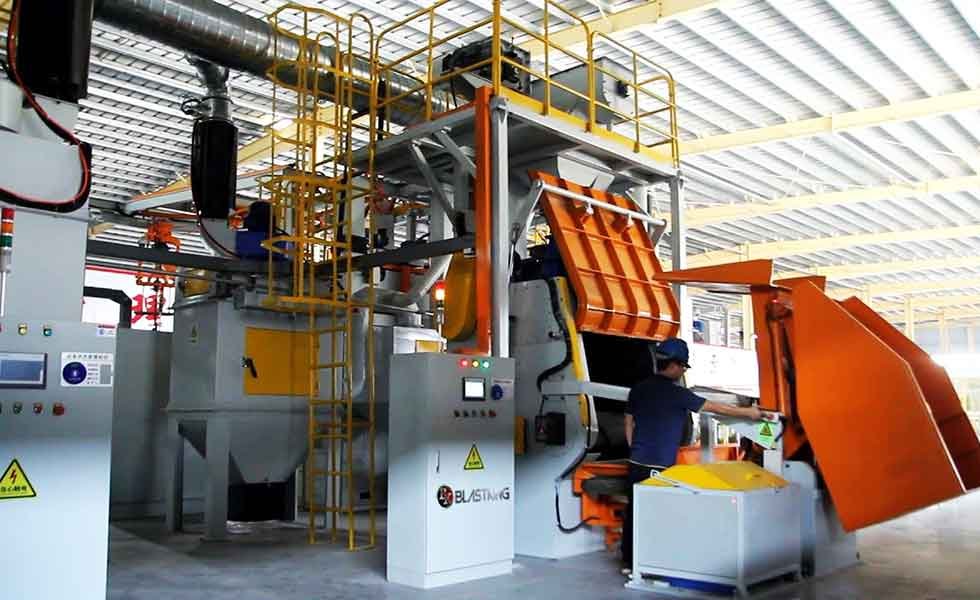
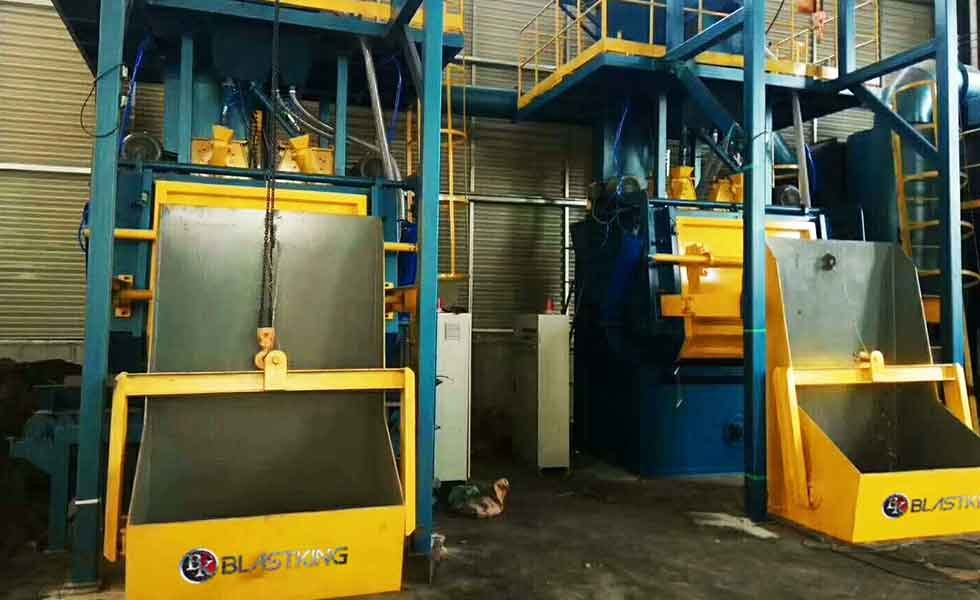
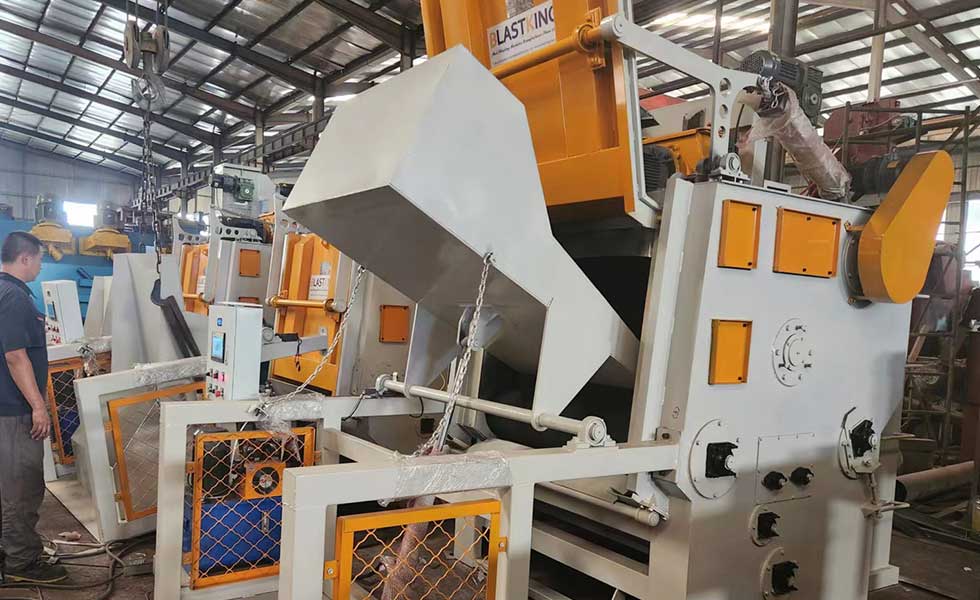
How the Magic Happens
Here’s the typical workflow in a tumble belt shot blasting machine:
-
Load the Parts: Manually, via forklift, or with automated systems—whatever suits your setup.
-
Blast & Tumble: The belt rotates, parts roll around, and high-speed abrasive particles work their magic.
-
Dust & Media Removal: Continued tumbling knocks off leftover media from tight corners.
-
Unload and Admire: Clean, uniform parts are discharged, ready for the next step.
Simple? Yes. Effective? Absolutely.
Say Goodbye to Rust, Burrs, and Production Bottlenecks
Features That Make a Real Difference
With BlastKing, it’s not just about cleaning parts. It’s about making your life easier:
-
High-Efficiency Blast Wheels: Faster cleaning with less abrasive consumption.
-
Choice of Belts: Rubber for delicate pieces, steel for heavy-duty applications.
-
Sealed Blast Chambers: Cleaner workplaces, healthier environments.
-
Optimized Drop Heights: Goodbye, part damage.
-
Easy Maintenance Access: Because nobody likes downtime.
And yes, custom configurations? We do that too.
Where You’ll Find Them Working
You’ll spot our tumble belt shot blasting machines everywhere:
-
Foundries removing sand and scale.
-
Forging plants descaling heat-treated parts.
-
Automotive shops deburring gears and suspension components.
-
Aerospace boosting fatigue strength with shot peening.
-
General metalworking prepping surfaces for coatings.
Some even handle non-metallic materials like composites. Talk about versatility.
Small Space? No Problem. Big Results in Compact Machines
Industry 4.0 and a Greener Future
We’ve packed our machines with smart tech: power monitoring, abrasive flow sensors, and predictive maintenance alerts. You’ll save energy, reduce waste, and keep production lean—all while meeting sustainability goals.
Why BlastKing Tops the Charts
Here’s what four decades in the industry taught us:
-
Off-the-shelf doesn’t work for everyone—so we customize.
-
Service matters as much as the machine—so we support you globally.
-
Innovation never sleeps—so we keep evolving.
With BlastKing tumble shot blasting machines, you’re not just buying equipment. You’re partnering with a team obsessed with your success.
Ready to Make Surface Prep Stress-Free?
Your parts deserve better. Your production line deserves faster, cleaner, and more cost-effective solutions. A BlastKing tumble belt shot blasting machine delivers all that—and then some.
Why not talk to us today? Let’s make surface preparation the easiest part of your job.
Don’t Let Outdated Machines Drain Your Budget
Basic Specification of Tumble Blasting Machines
Tumblast Machine with Rubber Belt
Type | MB100H | MB200H | MB600H | MB1000H | MB1500H | MB2000H | MB2800H |
---|---|---|---|---|---|---|---|
Productivity(t/h) | 0.3-0.8 | 0.6-1.2 | 1.5-2.5 | Â 3-5 | 3.5-6.5 | 5-9 | 7-12 |
Max advised load (kg) | 100 | 200 | 600 | 1000 | 1500 | 2000 | 2800 |
Drum Capacity (mm) | Φ480×500 | Φ650×600 | Φ1000×1100 | Φ1100×1100 | Φ1000×1530 | Φ1200×1530 | Φ1400×1530 |
Number of blast wheels | Â 1 | Â 1 | 1 | 2 | 2 | 2 | 2 |
Wheel power (kW) | Â 7.5 | 7.5/11 | 15 | Â 2x11 | Â 2x15 | Â 2x18.5 | Â 2x22 |
Dust collecting air volume (m3/h) | 1800 | 2200 | 5000 | 6000 | 8000 | 8000 | 12000 |
Total power (kW) | 10 | 12.6 | 19 | 38.67 | 52.57 | 68.07 | 82.37 |
Tumblast Machine with Steel Belt
Type | MB800G | MB1350G | MB3950G |
---|---|---|---|
Productivity(t/h) | 0.6-1.2 | Â 1.5-2.5 | Â 3-5 |
Single workpiece maxi. weight (kg) | 40 | 220 | 720 |
Max advised load (kg) | 800 | 1360 | 3950 |
Drum capacity (mm) | Φ1000×1100 | Φ1100×1245 | Φ1250×1780 |
Number of blast wheels | Â 1 | 2 | 2 |
Wheel power (kw) | 18.5 | 2x15 | 2x22 |
Dust collecting air volume (m3/h) | 3200 | 8000 | 12000 |
Total power consumption(kw) | 28.5 | 46.7 | 80 |
- The technical data is not binding and may be subject to change.
- Depending on the type of parts, production method, etc., further machine types and measurement specification sheets upon request.
Built to Keep Your Production Line Running
We deliver results
Our Happy Clients!
Ready to Make Surface Prep Effortless?
Tired of inefficient, slow, or inconsistent cleaning slowing your workflow?
Stop compromising. Invest in a BlastKing tumble belt shot blasting machine and transform your production line. Faster cleaning, stronger parts, lower costs — all in one machine. Request your demo or quote today!
Call us today at +86 135 8931 7685